Corresponding author: ZHANG Rong-chuang, E-mail: zhangrongchuang@126.com
滚齿加工广泛应用于外圆柱齿轮粗加工.现已经提出了许多滚齿加工物理仿真模型,其目的主要是用来帮助确定合理的加工参数,选择合理的滚刀设计参数,进而减少加工过程刀具磨损、齿面残余应力以及抑制加工过程中毛刺形成和提高齿面加工精度等.在所建立的物理模型中滚切力模型是其他物理模型的基础.
滚切力模型在实际加工仿真中的应用需要几何信息作为求解的边界条件.最初的滚齿加工仿真主要采用空间离散方法,然而这些方法由于所采用的简化策略以及精度原因并不适用于几何边界参数提取[1, 2, 3, 4, 5].基于实体的造型系统具有较高的几何建模精度和较强的材料去除仿真能力,是国内外学者普遍采用的加工仿真手段,同时也是保证瞬时几何边界参数提取精度的有效选择.Antoniadis基于CAD软件对刮齿加工过程进行 仿真,提取出刮刀切削刃上最大切削厚度与切削面积[6].Yip-Hoi等为实现端铣削力预测,基于实体造型技术,在构建出的CWE(cutter/workpiece engagement)上提取出端铣刀切削刃上切削厚度分布[7].Yang等利用实体建模布尔运算,在提取出的CWE上实现了多轴铣削过程切削厚度的计算[8].国内刘胤、倪其民等在球头铣刀三维铣削力仿真中,提出了以B-rep和CSG为基础的铣刀切角区间和切深区间几何提取方法[9, 10].
为满足滚刀加工仿真中动态滚切力精确预测,本文提出基于三维实体造型技术的滚齿切削厚度仿真计算方法;以直齿轮滚齿加工仿真为例,在以商用CAD软件NX的二次开发平台为基础的实体仿真系统上对该仿真计算方法予以实现.
1 滚齿坐标系定义实现滚齿加工,图 1所示为本文中所采用的数控滚齿机示意简图.
![]() |
图1 数控滚齿机示意简图 Fig. 1 The sketch map of CNC hobbing machines |
其中数控轴分别为:径向进给轴(Y轴);轴向进给轴(Z轴);切向运动轴(X轴);工作台回转轴(C轴);滚刀主轴回转轴(B轴);刀架转角回转轴(A轴)
为了方便地表示滚齿切削厚度的仿真计算,建立如图 1,图 2所示的辅助坐标系.
工件坐标系XpYpZp:固定于工作台上表面,Zp为工件轴线,Yp为加工齿轮齿槽中线,Xp,Yp,Zp构成左手笛卡尔坐标系;p为工件旋转过的角度.
滚刀坐标系XhYhZh:造型空间中通过轴向间距Δa和径向角度差Δθ来描述滚刀工作刀齿与切削中心刀齿之间相对位置关系的坐标系,与滚刀固定连接.Xh为滚刀轴线,Yh位于展成中心刀齿齿廓曲线对称中心线,Xh,Yh,Zh构成左手笛卡尔坐标系,如图 3所示;h为滚刀旋转过的角度,Γ为滚刀安装角.
![]() |
图2 坐标系定义 Fig. 2 Coordinate system definition |
![]() |
图3 滚刀坐标系 Fig. 3 Hob coordinate system |
滚刀N号刀齿坐标系XnYnZn:用以描述滚切力建模时滚刀刀齿前刀面切削刃上任意一点位置的坐标系.Xn平行于滚刀轴线,Yn为滚刀刀齿前刀面曲线对称中心线,Xn,Yn,Zn构成右手笛卡尔坐标系,如图 4所示;K为刀齿顶刃中点,P为与坐标系原点距离为L的点.
![]() |
图4 滚刀N号刀齿坐标系 Fig. 4 N tooth coordinate system |
坐标系XrYrZr,XfYfZf为参考坐标系,分别与切向进刀装置、机床床身固定连接.
2 几何边界参数定义图 5所示为典型滚刀及其刀齿几何模型示意图.刀齿切削刃位于滚刀刀齿前刀面上,由直线刃(顶刃、两个侧刃)和两个圆弧刃组成.
![]() |
图5 滚刀及其刀齿几何模型 Fig. 5 Geometric model of hob tooth |
切削力模型在实际加工仿真中的应用需要几何信息作为求解的边界条件,因此几何边界参数的定义主要取决于所采用的切削力学模型.本文中为了计算滚切力,将滚刀刀齿切削刃离散为微元,并假设参与切削的每一微元切削刃均为直齿条件下建立的,作用在刀齿上的总滚切力则等于对所有参与切削的微元切削刃的切削力矢量求和.作用在切削微元上的空间滚切力分解为微切向力ΔFt,微径向力ΔFf,微轴向力ΔFr,其表达式为[11]
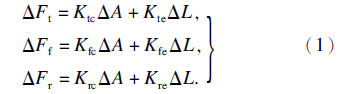
滚齿加工中,CWE定义为滚刀刀齿与未变形切屑接触区域.图 6所示为N号刀齿坐标系XnYnZn下的CWE示意图,r为圆弧刃半径,h为离散位置切削厚度,αc为刀齿齿形角.本文中直线刃采用滚刀轴向等间距Δc方式进行离散,离散后的切削微元近似为直角梯形,其面积为ΔA=Δb×(hm+hm+1)/2,微元刀-屑接触长度ΔL=Δb(顶刃Δb=Δc,侧刃Δb=Δc/sinαc;圆弧刃采用等角度dθ方式进行离散,离散后的切削微元由一条圆弧、两条直线和一条样条曲线组成,其面积为ΔA=r2×dθ/2-(r-hm)×(r-hm+1)×sin(dθ),微元刀-屑接触长度为ΔL=r×dθ.
由上述内容可知,ΔL取决于切削刃微元划分数量,ΔA可以通过微元切削厚度进行数值计算获取,因此切削厚度才是几何边界提取过程中的重要几何参数.
![]() |
图6 CWE及切削微元 Fig. 6 CWE and cutting element |
由于切屑是刀齿前刀面扫掠体与当前瞬时齿廓实体的交集,因此包含了切削力计算所需要的几何参数.本文采用访问CWE的方法提取几何边界参数.首先导入未变形切屑几何实体,从未变形切屑识别包含切削几何参数信息的CWE,在CWE上进行切削厚度提取.
3.1 CWE构建滚齿加工中,刀齿前刀面运动实现切屑去除过程,因此CWE可以理解为刀齿前刀面所在平面与未变形切屑的交线按照顺序连接所形成的封闭区域.滚齿加工过程仿真中假设工件静止不动,滚刀绕其自身轴旋转的同时,也绕着滚刀轴作螺旋运动,所得到的未变形切屑是在工件坐标系XpYpZp下的几何实体模型.导入切屑几何实体后,建立滚刀刀齿前刀面瞬时旋转位置下的所在平面,即前刀面平面.确定前刀面平面的位置,首先确定刀齿在切削旋转角度内的位置,再由刀齿坐标系下的P,K及刀齿坐标系原点On三点,经过滚刀坐标系XhYhZh,参考坐标系XrYrZr,XfYfZf的坐标转换,转换为工件坐标系XpYpZp下的三点,通过其确定前刀面平面位置.图 7所示为工件坐标系XpYpZp下的切屑几何实体,以及一系列前刀面所在平面,通过二者之间的求交运算,得到包含切削几何参数的CWE.
3.2 切削厚度仿真计算图 8所示为切削厚度提取过程示意图,CWE位于滚刀刀齿前刀面平面;直线刃部分用一组垂直于直线刃、间距为Δb的有界平面与包含CWE曲线求交,得到两个交点,交点之间的距离就是该平面所处轴向位置的切削厚度h,有界平面之间的间距Δb即是微元刀-屑接触长度ΔL,如图 9a所示.圆弧刃部分用一组垂直于弧线刃的等角度的有界平面与包含CWE曲线求交,得到两个交点,交点之间的距离就是该平面所处轴向位置的切削厚度h,有界平面之间的夹角所对应的弧长Δb即是微元刀-屑接触长度ΔL,如图 9b所示.
![]() |
图7 仿真过程中CWE形成 Fig. 7 CWE development process |
![]() |
图8 切削厚度提取示意图 Fig. 8 Extraction of chip thickness |
![]() |
图9 切削厚度 Fig. 9 Chip thickness (a)—直线刃; (b)—圆弧刃. |
选取模数mn=3,齿数Zp=36,进给量f=1mm/rad,压力角α=20°,滚刀采用国家标准2型齿轮滚刀,进行加工仿真.以2号刀齿,即展成位置为2时去除的未变形切屑为研究对象,将刀齿在其旋转180°内等分成180份,确定前刀面平面所在的180个旋转位置,直线刃离散间距Δc=0.004075mm,圆弧刃离散角度dθ=0.7°;适当地减小Δc,dθ可以提高切削厚度的提取精度.图 10所示为经过几何边界参数提取后切削厚度h分布示意图.
![]() |
图10 提取后切削厚度分布 Fig. 10 The distribution of chip thickness |
1) 依据所采用的切削力模型,定义了滚刀几何边界参数,并将其转化为切削厚度,即直接几何边界参数为变量的表达式.
2) 以CWE为未变形切屑与切削厚度的纽带,通过在CWE上的几何仿真计算,实现了滚刀直线刃与圆弧刃上的切削厚度提取.
3) 基于实体造型的滚齿切削厚度仿真计算为动态滚切力等物理模型应用奠定了基础;同时本文所提出的方法也适用于刮齿、铣削等切削力模型几何边界参数提取.
[1] | Klocke F,Gorgels C,Schalaster R,et al.An innovative way of designing gear hobbing processes[C]//Proceedings of the International Conference on Gears.Munich,2010:393-404.(![]() |
[2] | Bouzakis K D,Lili E,Michailidis N,et al.Manufacturing of cylindrical gears by generating cutting processes:a critical synthesis of analysis methods[J].CIRP Annals—Manufacturing Technology,2008,57(2):676-696. (![]() |
[3] | Umezaki Y,Ariura Y.An application of numerical analysis of hobbing to hob wear,cutting force and gear tooth topography[C]//World Congress on Gearing and Power Transmission.Paris,1999:1833-1838.(![]() |
[4] | Abood A M,Bicker R,Pennell T.An analysis of cutting forces in gear hobbing[J].VDI-Berichte,2002,1665:255-262.(![]() |
[5] | Antoniadis A,Vidakis N,Bilalis N.Fatigue fracture investigation of cemented carbide tools in gear hobbing,part 1:FEM modeling of fly hobbing and computational interpretation of experimental results[J].Journal of Manufacturing Science and Engineering,2002,124(4):784-791.(![]() |
[6] | Antoniadis A.Gear skiving—CAD simulation approach[J].Computer-Aided Design,2012,44(7):611-616.(![]() |
[7] | Yip-Hoi D,Huang X.Cutter/workpiece engagement feature extraction from solid models for end milling[J].Journal of Manufacturing Science and Engineering,2006,128(1):249-260.(![]() |
[8] | Yang Y,Zhang W,Wan M,et al.A solid trimming method to extract cutter-workpiece engagement maps for multi-axis milling[J].The International Journal of Advanced Manufacturing Technology,2013,68(9/10/11/12):2801-2813.(![]() |
[9] | 刘胤.实体法铣削力仿真中几何参数提取及算法优化的研究[D].北京:清华大学,2005.(Liu Yin.Research on the geometric parameters extraction and algorithm optimization of solid modeling based milling force simulation [D].Beijing:Tsinghua University,2005.)(![]() |
[10] | 倪其民,李从心,阮雪榆.基于实体造型的球头铣刀三维铣削力仿真[J].上海交通大学学报,2001,35(7):1003-1007.(Ni Qi-min,Li Cong-xin,Ruan Xue-yu.Cutting forces simulation of ball-end milling based on solid modeling[J].Journal of Shanghai Jiaotong University,2001,35(7):1003-1007.)(![]() |
[11] | Yusuf A.Manufacturing automation:metal cutting mechanics,machine tool vibrations,and CNC design[M].New York:Cambridge University Press, 2012.(![]() |