2. 重庆大学 复杂煤气层瓦斯抽采国家地方联合工程实验室, 重庆 400030
2. National & Local Joint Engineering Laboratory of Gas Drainage in Complex Coal Seam, Chongqing University, Chongqing 400030, China.
Corresponding author: ZHANG Xin-wei, E-mail:cquzhangxinwei@163.com
近年来,水射流割缝技术被广泛应用在我国煤矿井下[1].该技术通过高压水射流对煤体进行切割,增大了煤体暴露面积,增加煤层裂隙率,最终达到提高瓦斯抽采率的目的[2].然而,当现场实施割缝遇到硬煤层时,纯水射流无法实现有效切割,致使水射流割缝失效.为了解决这一问题,林柏泉等[3]提出了磨料射流割缝技术,并通过现场实验证实了高压磨料射流具有更强的割缝能力,增透效果明显优于纯水射流.但是该技术并没有被大量地应用于煤矿井下,原因在于现场采用的前混合磨料射流技术难以实现磨料的连续添加,影响了割缝效果[4, 5].为此,左伟芹等[6]对此进行了大量研究,优化后的设备虽实现了磨料的连续添加,但工艺较复杂,难以在煤矿井下推广.同时,后混合磨料射流装置要求在喷嘴处设置磨料供给通道,由于割缝器需通过钻孔到达煤层,尺寸受到限制,无法增加该磨料供给通道,因此后混合磨料射流装置亦无法在煤矿井下水射流割缝中得到应用.
针对上述技术问题,作者基于引射原理[7],采用前后双喷嘴结构,提出一种煤矿井下自吸式磨料射流割缝喷嘴,该喷嘴通过吸入割缝过程中产生的煤粒形成磨料射流,进而提高割缝能力.而喷嘴的结构决定割缝的效果,因此本文通过数值模拟研究自吸式磨料射流喷嘴结构对喷嘴中煤粒和液固两相流动的影响,从而选出最优结构,并在实验室进行模拟割缝实验,验证其割缝效果.
1 自吸式磨料射流喷嘴结构割缝器与自吸式磨料射流喷嘴结构如图1所示.进行割缝时,高压水经过前喷嘴形成射流,射流的高速流动在混合腔的中心两侧形成负压,在该负压的作用下,割缝产生的煤粒被卷吸进入混合腔,通过对煤粒加速,煤粒与主射流充分混合,形成磨料射流.
![]() | 图 1 自吸式磨料射流喷嘴结构 Fig. 1 Structure of self-priming abrasive jet nozzle1—前喷嘴; 2—吸入口; 3—混合腔; 4—后喷嘴. |
该喷嘴的主要结构参数有前后喷嘴直径d1,d2,吸入口直径d3;前喷嘴、混合腔和后喷嘴的长度L1,L2,L3.后喷嘴为辅助加速,射流主要通过前喷嘴形成,因此,d1取决于射流的流量和压力.因煤层割缝器与钻头组合使用,割缝器上除喷嘴外还需有一个轴向辅助钻进的水出口,按照经验该出水口的流量与喷嘴流量相当时最有利于钻孔排渣.大部分矿用乳化泵额定流量为200 L/min,因此分到割缝喷嘴的最大流量为100 L/min.根据伯努利方程计算得到d1为3.075 mm,综合考虑加工因素,确定d1为3 mm.根据吸入原理,吸入口直径为前喷嘴直径的3~5倍为最佳,而由于尺寸受限,设计直径达不到最佳值,因此根据吸入口直径大于磨料粒径3倍的原则确定d3为 1 mm.
常用割缝喷嘴总长受到割缝器尺寸的限制,因此前喷嘴长度在保证射流稳定的前提下取最小值,确定L1为6 mm.L2和L3的具体长度需要根据二者对割缝效果的影响程度合理分配.
2 自吸式磨料射流喷嘴特性根据引射原理,可知L2和d2及L3直接影响吸入量和磨料加速效果(即射流传递给磨料的能量),决定喷嘴性能及割缝能力.由于喷嘴的尺寸比较小并且内部受力十分复杂[8],因此建立的煤粒运动方程存在复杂的非线性关系,难以得到解析解;并且喷嘴结构参数的具体值难以用实验方法得到.因此,本文使用数值模拟方法对自吸式磨料射流喷嘴特性进行分析,对其结构进行优化设计.
2.1 物理模型在d1=3 mm,d3=1 mm,L1=6 mm的前提下,进行两组模拟实验:①设定d2=5 mm,L2=3,4,5,6,7 mm,L3=12 mm,研究L2对吸入效果的影响;②根据①得到的L2值,设定d2=4,5,6,7,8,9,10 mm,L3=9,10,11,12,13,14,15 mm,建立物理模型,研究d2和L3对吸入效果的影响.
喷嘴中煤粒的加速过程涉及复杂的液固两相流动问题,本文建立模型时,对实际情况进行适当简化:液体视为不可压缩的连续介质;煤粒视为相同粒径的刚性颗粒;液体与煤粒和外界没有热量交换;不考虑煤粒之间相互作用.
2.2 控制方程在由流体和煤粒组成的弥散多相流体系中,将流体相视为连续介质,煤粒视作离散介质处理.其中,连续相的数学描述采用欧拉方程,求解时均N-S方程得到速度等参量;分散相采用拉格朗日方法描述,通过对大量质点的运动方程进行积分运算得到其运动轨迹.
1) 连续相控制方程.喷嘴内实际流体均具有黏性,连续相水的流动可以通过增加流体与煤粒相互作用源相的时均N-S方程,建立标准k-ε双方程紊流数学模型.在空间直角坐标系下,其控制方程组如下.
连续性方程为
时均运动方程为
2) 颗粒相控制方程.由于进行水力割缝时水流量大,煤粒体积分数较低,约为5%~9%.因而,液固两相间仅考虑双向耦合,忽略煤粒间的碰撞行为.
为简化分析,本文只考虑主要的重力与浮力的合力、阻力、压力梯度力、虚假质量力,忽略次要作用力.通过积分Lagrangian参考系下的煤粒的运动方程计算其运动轨迹.由煤粒的惯性与受力平衡知,煤粒运动方程为
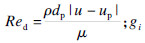
在一个时间步Δt内,一个控制容积内的连续相与分散相的动量交换等于煤粒的动量变化量:

根据喷嘴结构,建立物理模型并划分网格,采用结构化网格形式,并在壁面及混合腔对网格进行加密.连续相的入口、吸入口、出口均取为压力边界,入口压力为28 MPa,吸入口、出口压力为0 MPa,壁面满足无滑移绝热条件,且与煤粒完全弹性碰撞.在吸入口断面上,颗粒相采用面射流源产生,密度设为1 330 kg/m3(烟煤真密度),粒径为1 mm,体积分数为8%.
求解采用相耦合SIMPLE算法,离散格式均采用二阶迎风格式,对控制方程进行数值计算.
2.4 模拟结果与分析模拟结果显示:在前喷嘴射流高速流动时,周围的煤粒被卷吸进入混合腔,并得到加速,之后煤粒与主射流充分混合,该结构设计合理,可以连续吸入割缝产生的煤粒形成磨料射流,提高了割缝能力.
分析处理各个模拟结果图,发现在不同的工况下,煤粒的运动轨迹及出口速度不尽相同,但都经历了典型的3个加速阶段:吸入口加速段、混合腔加速段和后喷嘴加速段,如图2所示.该模拟结果图的工况: d1=3 mm,d2=5 mm,L2=3.5 mm,L3=15 mm;以此来分析煤粒的加速过程及液相对煤粒的作用机理.
![]() | 图 2 煤粒群迹线模拟结果 Fig. 2 Simulation result of swarm trace of coal particle1—吸入口加速段; 2—混合腔加速段; 3—后喷嘴加速段. |
选取图2中某单颗煤粒的迹线,横轴表示煤粒自吸入后移动的距离(标量),纵轴表示迹线上各点的速度,如图3所示.可知,在液相的卷吸作用下,煤粒随水流由吸入口进入喷嘴内部,并在吸入口段(0~0.007 m)得到第一次加速,至24 m/s;煤粒进入混合腔(0.007~0.012 m)后,与高速射流发生动量交换,速度迅速增加至69 m/s;随后,煤粒与液相在后喷嘴(0.012~0.026 m)中得到充分混合,煤粒速度进一步增加,在后喷嘴出口达到最大值84 m/s.分别对应于图2中的3个加速阶段:吸入口加速段、混合腔加速段和后喷嘴加速段.
![]() | 图 3 单颗煤粒加速过程 Fig. 3 Fig.3 |
煤粒是在液相的作用下被吸入并得到加速.液相由前喷嘴形成高速射流,喷嘴出口速度为235 m/s,到与煤粒混合之前达到最大速度249.8 m/s,之后,射流速度便逐渐降低.表明在吸入口加速段中,是由射流高速流动形成的负压作用实现对煤粒加速;而在混合腔加速段和后喷嘴加速段中,射流与吸入的煤粒充分混合并进行动量交换,传递能量使煤粒加速,导致射流速度降低.
3 自吸式磨料射流喷嘴参数根据模拟结果,研究L2,d2,L3对吸入口流体的平均速度及后喷嘴出口煤粒平均速度的影响规律,从而获得结构参数的最优值.
对数值模拟第①组数据进行处理,发现L2的小范围增加,导致吸入口流体的平均速度小幅度升高,在11.2~12.5 m·s-1之间,以及后喷嘴出口煤粒平均速度在58.4~60.1 m·s-1之间上升.总之, L2对吸入效果影响很小.
根据数值模拟第②组数据,得到不同后喷嘴长度下,后喷嘴与前喷嘴直径比(d2/d1)对吸入口流体平均速度的影响规律,如图4所示.
![]() | 图 4 吸入口平均速度与d2/d1关系 Fig. 4 Relationship between suction average speed and d2/d1 |
分析可知,在同等压力条件下,喷嘴吸入口流体平均速度随着d2/d1的增大先增大后减小,当d2/d1为2.3~2.7时,被吸入流体的平均速度最大.由于煤粒在吸入口外均匀分散于水介质中,流体被吸入的速度决定了吸入量的大小.因此,d2/d1为2.3~2.7时,对应吸入量最大.
后喷嘴出口煤粒平均速度与d2/d1的关系如图5所示.煤粒的平均速度随d2/d1的增大先减小后增大,当d2/d1为2.7时达到最小.而磨料射流的切割能力[9]与磨料体积分数和磨料速度均相关.图4和图5表明,速度分别在d2/d1=2.7时达到最大值和最小值,因此无法据此优选出最优的后喷嘴与前喷嘴直径比.
![]() | 图 5 煤粒平均速度与d2/d1关系 Fig. 5 Relationship between coal particle speed and d2/d1 |
从能量角度出发,综合图4和图5的数据,得到煤粒所获得的功率与d2/d1的关系,如图6所示.由图可知,当d2/d1为1.5~1.7时,煤粒获得的能量最大.
由图4~图6可知,吸入量、煤粒速度和煤粒获得能量均是随L3的增大而增大.
![]() | 图 6 煤粒所获功率与d2/d1关系 Fig. 6 Relationship between coal particle power and d2/d1 |
根据以上结果可以发现,结构参数d2对吸入量与加速效果影响最大,其次是L3,而L2的影响最小可忽略.常规割缝喷嘴长度为24.5 mm,因此在有限的尺寸内,L3尽可能取大,L2尽可能取小.综上,自吸式磨料射流喷嘴最优结构参数:d1=3 mm,d2=5 mm,L2=3.5 mm,L3=15 mm.
4 自吸式磨料射流割缝实验以最优结构参数加工出自吸式磨料射流喷嘴,进行模拟割缝实验,并将其与传统喷嘴进行割缝能力的对比,以验证自吸式磨料射流割缝的效率.
4.1 实验设备及步骤实验选用ZY-750型煤矿用液压钻机;试件箱尺寸为1 m×1 m×1 m;试件箱由上下两半扣合在一起,便于实验过程中打开记录数据.实验系统连接如图7所示.
![]() | 图 7 实验系统连接示意图 Fig. 7 Assembling diagram of experiment system 1—水箱; 2—乳化泵; 3—溢流阀; 4—压力表; 5—高压密封水尾;6—液压钻机; 7—煤层割缝器; 8—钻头; 9—试件箱; 10—缝槽. |
采用两种配比的煤粉、水泥浇筑两个不同强度试件,代表软煤及硬煤,测得其单轴抗压强度分别为4.13和13.21 MPa.
管路连接好后,推进钻机至合适位置,调整钻机转速为30 r/min;开启高压泵,待其稳定后升压至28 MPa;每隔60 s停泵并记录切割长度和宽度,直至试件被冲穿或者切割长度不再随时间而增加.
4.2 实验结果及分析与传统纯水射流相比,随着煤粒的吸入,射流性能的变化必然引起切割深度和宽度的变化.切割实验结果如图8所示.
![]() | 图 8 实验结果图 Fig. 8 Experimental results(a)—硬煤; (b)—软煤. |
图9为自吸式磨料射流喷嘴和传统喷嘴在不同模拟煤体中的切割深度、宽度随切割时间的变化曲线.实验结果表明:对于模拟软煤层,自吸式磨料射流喷嘴的切割深度约为传统喷嘴的1.4倍,切割平均宽度为传统喷嘴的1.2倍以上;对于模拟硬煤层,自吸式磨料射流喷嘴的切割深度为传统喷嘴的1.8倍以上,切割平均宽度为传统喷嘴的1.4倍以上.与传统喷嘴相比,自吸式磨料射流喷嘴具有更高的切割能力,用于硬煤层割缝具有显著的优势.
![]() | 图 9 喷嘴切割对比 Fig. 9 Comparison of nozzle cutting |
1) 基于引射原理,设计出一种自吸式磨料射流割缝喷嘴,可以有效吸入割缝产生的煤粒形成磨料射流,提高了割缝能力.煤粒在喷嘴内经历3个加速阶段:吸入口加速段、混合腔加速段和后喷嘴加速段.
2) 自吸式磨料喷嘴最优结构:前喷嘴直径为3mm,后喷嘴直径为5mm,混合腔长度为3.5mm,后喷嘴长度根据割缝器尺寸取最大值.
3) 实验室割缝实验结果表明:相比原纯水射流割缝技术,自吸式磨料射流割缝器切割软煤时,割缝深度增加约40%,平均宽度增加约20%;切割硬煤时,割缝深度增加约80%,平均宽度增加约40%.
[1] | Lu Y Y,Liu Y,Li X H,et al.A new method of drilling long boreholes in low permeability coal by improving its permeability [J].International Journal of Coal Geology,2010,84(2):94-102.(![]() |
[2] | Wei G Y,Shan Z Y,Zhang Z M,et al.Research on hydraulic slotting technology controlling coal-gas outbursts [J].Journal of Coal Science and Engineering (China),2008,14(1):67-72.(![]() |
[3] | 林柏泉,吕有厂,李宝玉,等.高压磨料射流割缝技术及其在防突工程中的应用[J].煤炭学报,2007,32(9):959-963.(Lin Bai-quan,Lyu You-chang,Li Bao-yu,et al.High pressure abrasive hydraulic cutting seam technology and its application in outbursts prevention[J].Journal of China Coal Society,2007,32(9):959-963.)(![]() |
[4] | Liu L H,Cao H,Zou C Q,et al.Supply abrasive system of premixed abrasive jet and derusting application[J].Applied Mechanics and Materials,2012,217(1/2/3):2033-2037.(![]() |
[5] | Hiavac L M,Hiavacova I M,Gembalova L,et al.Experimental method for the investigation of the abrasive water jet cutting quality[J].Journal of Materials Processing Technology,2009,209(20):6190-6195.(![]() |
[6] | 左伟芹,卢义玉,夏彬伟,等.前混合磨料射流新型连续加砂系统设计与实验[J].应用基础与工程科学学报,2013,21(2):328-335.(Zuo Wei-qin,Lu Yi-yu,Xia Bin-wei,et al.System design of continuous feeding abrasive for pre-mixed abrasive jet and its experiment [J].Journal of Basic Science and Engineering,2013,21(2):328-335.)(![]() |
[7] | Gagan J,Smierciew K,Butrymowicz D,et al.Comparative study of turbulence models in application to gas ejectors[J].International Journal of Thermal Sciences,2014,78(11):9-15.(![]() |
[8] | Jafar R H M,Spelt J K,Papini M.Numerical simulation of surface roughness and erosion rate of abrasive jet micro-machined channels [J].Wear,2013,303(1/2):302-312.(![]() |
[9] | Oh T M,Cho G C.Characterization of effective parameters in abrasive water jet rock cutting [J].Rock Mechanics and Rock Engineering,2014,47(2):745-756.(![]() |