2.太钢股份有限公司 不锈冷轧厂, 山西 太原 030003
2. Stainless Steel Cold Rolling Mill, Shanxi Taigang Stainless Steel Co., Ltd., Taiyuan 030003, China.
Corresponding author: TONG Wei-ping, professor, E-mail: wptong@mail.neu.edu.cn
α″-Fe16N2相是一种不稳定的铁氮化合物,具有优越的磁性能,引起了人们的广泛关注.1972年,Kim和Takahashi在进行由氮气中蒸发Fe膜的实验中首先发现α″-Fe16N2相具有极高的饱和磁化强度[1].1990年,Komuro利用分子束外延技术在Fe/Ga0.8In0.2As基体上制得α″-Fe16N2相的单晶薄膜[2],检测确定其饱和磁化强度为2.8~3.0T,这也是目前可查的最高的检测结果.随后,世界各地的科研人员通过离子注入法[3]、溅射镀膜法[1]、等离子蒸发镀膜法[4]、机械合金化法、射频磁控溅射法[5]、气固反应法等方法制备出各种薄膜状或粉末状的样品.这些样品在经过检测后,均未得到与Komuro相同的实验结果,其中最好的检测结果也仅为饱和磁化强度达到2.4T.
目前制备块状α″-Fe16N2磁性材料存在许多技术上的困难,难以获得单相块状α″-Fe16N2相材料.通过气固反应法在块状铁基材料中析出α″-Fe16N2相可以制备出铁基α″-Fe16N2相磁性材料.Tang等分别以非晶Fe92B8材料[6]和非晶Fe84.8N7.8B7.4材料[7]为基质制备α″-Fe16N2相,试样厚20μm,α″-Fe16N2相的体积分数为54 % ,饱和磁化强度为2.35T.Niizuma等[8]以纯铁进行实验,试样厚20μm,α″-Fe16N2相的体积分数为30.3 %.就目前的实验结果来看,铁基α″-Fe16N2相材料的厚度普遍低于30μm.研制较厚的铁基α″-Fe16N2相磁性材料成为目前的主要研究方向.
本文主要研究了块状铁基α″-Fe16N2材料的制备方法,首先采用气固反应法在块状纯铁表面进行气体渗氮,制备出高含氮量的氮化铁材料,再经退火处理,使氮元素在铁基体中均匀扩散,最后通过高温淬火及低温回火,在块状纯铁材料中制备出α″-Fe16N2相质量分数达到50.57 % 、比饱和磁化强度达到223.6A · m2/kg的磁性材料.
1 实验材料和实验方法实验原始材料采用尺寸为15mm×15mm×0.06mm的块状纯铁,纯度为99.95 %.纯铁材料经过923K,120min真空退火.用60#~1000#金相砂纸打磨抛光并用丙酮超声波清洗.
渗氮处理是在管式炉中通入流动的氨气,550℃渗氮处理3h.将经过渗氮处理的试样封入充满氩气的石英管中,在640℃下退火处理2h.将样品在680℃熔融盐中保温5min后水冷淬火并迅速放入液氮中进行深过冷处理.随后,使用220-00AB型台式电热干燥箱,在140~170℃不同时间下进行回火处理.
分别对渗氮、退火、淬火及回火后的样品进行研磨、抛光并腐蚀后用Leica DM/T-400型金相显微镜进行观察.用荷兰PANalytical B.V X′Pert Pro PW3040/60型X射线衍射仪进行物相分析,实验采用Cu靶(0.154056nm),管压为40kV,管流为40mA,进行30°~90°扫描.部分样品用Lakeshore 7407型VSM测试其磁滞曲线,检测时,最大磁场加到1T.
2 结果与讨论 2.1 块状纯铁的渗氮图 1a所示为样品经过渗氮处理后的横截面金相照片.根据纯铁渗氮理论,经过渗氮处理后的试样会发生分层现象,由外至内分别为化合物层、扩散层和基体层.从图 1a中也可以观察到类似现象,最外层白色物质约厚10μm,为化合物层;内部为基体层,厚度约为40μm.在基体层与化合物层交界位置,分布着针状析出相,属扩散层,这些针状析出相深入基体层的深度为40μm.图 1b所示为样品的XRD图谱.可以看出,样品表面的相组成主要为ε-Fe2-3N相,基体层的主要成分为α-Fe(N)相.在基体层与化合物层交界位置分布着的针状析出相,其成分应为γ′-Fe4N相.一般情况下,由于γ′-Fe4N相的扩散系数低于ε-Fe2-3N相,而且γ′-Fe4N相区很窄,渗氮产生的γ′-Fe4N相层很薄,甚至无法出现.试样中出现的针状γ′-Fe4N相应该是在渗氮结束后的冷却阶段,从α-Fe(N)相晶界处析出的薄片状γ′-Fe4N相.另外,可以观察到化合物层边缘呈波浪状,这是由于扩散形核具有不均匀性.
![]() |
图1 片状纯铁渗氮截面金相照片及XRD图谱 Fig. 1 Metallograph and XRD spectrum of nitriding pure iron sheet |
图 2a所示为试样经过退火后的截面金相照片.观察照片依旧可以发现明显的分层现象,最外层的厚度与图 1a所示相比有明显的增厚,达到25μm,但形貌却不同.图 1a中最外层为灰色化合物层,图 2a中的最外层则为黑白相间物质,在黑色物质的外部有白色物质包裹.图 2b为试样经过退火处理后的XRD图谱.通过分析可知,退火后的试样表层主要由α-Fe(N)相和少量的γ′-Fe4N相组成,渗氮试样中的ε-Fe2-3N相消失.这是由于退火过程促进了N原子的均匀化扩散,化合物层ε-Fe2-3N相中的N 原子向基体层扩散并与之反应生成大量的γ′-Fe4N相.
![]() |
图2 退火试样的金相照片及XRD图谱 Fig. 2 Metallograph and XRD spectrum of annealed samples |
图 3a为退火试样淬火并深冷处理后的样品截面微观组织照片.可以看到,样品的横截面主要分为三部分:最外层厚度为5~10μm,颜色较深.次外层颜色略浅,其中有明显的竹叶形片状组织和白色片状组织;竹叶形片状组织大小不一,相互之间不平行,其中往往有一片贯穿面积较大的,周围分布有较小的竹叶形组织,越接近表面处片状越小.内层为浅色均匀组织,次外层与 内层有明显的边界.图 3b为淬火样品的XRD图谱,分析可知,淬火样品中主要为α′-Fe(N)相和γ-Fe(N) 相.在XRD谱中50°左右的位置,发现残余奥氏体的次强峰.残余奥氏体的最强峰与马氏体的最强峰对应的角度接近,二者重合在一起而无法准确分辨,但根据次强峰的峰值可推测样品中残余奥氏体的含量很低.据此认为,次表层的竹叶形片状组织为含氮马氏体,即α′-Fe(N)相,之所以呈竹叶形是由于试样磨面与空间呈凸透镜形态的片状马氏体相截.白色的片状组织即为残余奥氏体.马氏体在越接近表面处片状越小,是由于表层含氮较高,形核率较大,使晶粒更细小的缘故.最外层形貌均匀的深色组织可能是含氮较高的化合物.淬火后再结晶过程中新相形成晶核需要很大的氮过饱和度,故这种新晶核不能在奥氏体内部生长,只有在表面才有足够的氮过饱和度来支持新相晶核的生成.当然,这种组织也可能是由于淬火保温时间较短而保留的未溶氮化物.基体内未见针状氮化物的产生,是由于冷却时间太短不足以析出针状氮化物.
![]() |
图3 淬火试样的金相照片及XRD图谱 Fig. 3 Metallograph and XRD spectrum of quenched samples |
对淬火试样进行低温回火处理,各试样的XRD图谱如图 4.对图 4a分析可知,当回火温度在140~160℃之间时,回火产物的主要组成相为α-Fe(N)相和α″-Fe16N2相.当回火温度达到170℃时,产物中α″-Fe16N2相消失,同时出现γ′-Fe4N相.为比较不同温度回火处理时样品中α″-Fe16N2相含量,根据各样品的XRD图谱采用RIR法计算各样品中各相的质量分数:
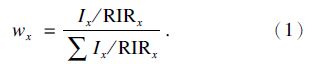
对比观察图 4a和图 4b可以发现,对150℃回火1.5h的试样延长回火时间后,产物中α″-Fe16N2相的质量分数有所增加.但是当回火时间达到13.5h时,样品中α″-Fe16N2相的含量急剧减少,同时XRD图谱中出现了γ′-Fe4N相的峰,说明已经生成了γ′-Fe4N相.根据式(1)计算图 4b各试样中α″-Fe16N2相的质量分数如表 1.
![]() |
图4 回火试样的XRD图谱 Fig. 4 XRD spectra of samples (a)—不同回火温度; (b)—不同回火时间. |
![]() |
表1 不同回火时间各试样中α″-Fe16N2相的质量分数 Table 1 Mass fractions of α″-Fe16N2 phase in the samples with different tempering time |
从表 1 中可知150℃回火4.5h制备得到的块状铁基α″-Fe16N2相材料最优,α″-Fe16N2相的质量分数可达到50.57 %.当回火时间大于4.5h,样品中的α″-Fe16N2相急剧减少.但140℃回火25.5h试样中α″-Fe16N2相的质量分数为48.99 % ,仅低于150℃回火4.5h的试样.尽管其回火时间长于其他试样,达到25.5h,但是并未导致试样中α″-Fe16N2相含量的大幅增加.
图 5为经过不同处理后试样的磁滞回线.从图 5中可以看出,不同的样品在磁场达到0.4T时磁化强度基本达到饱和.纯铁和γ′-Fe4N相为常见的铁磁性材料的主要成分,它们的饱和磁化强度Ms值分别为218A · m2/kg和186A · m2/kg. 因此可知淬火并深冷处理后试样的Ms低于纯铁 的相应值,此时α″-Fe16N2相尚未析出,样品中的主要成分为α′-Fe(N)相.图 5b为150℃回火 处理4.5h后试样的磁滞回线,此时样品饱和磁化强度Ms远高于纯铁,达到223.6A · m2/kg;矫顽力Hc为17.3×10-4T.这主要是由于此温度下α″-Fe16N2相已开始析出.图 5c为150℃回火处理13.5h后试样的磁滞回线,此时样品的Ms值相比回火处理4.5h样品的Ms值略有下降.前述测试中也发现,此时样品中的α″-Fe16N2相含量对比4.5h回火处理样品中含量有所减少.可能是由于样品中少量α″-Fe16N2相发生分解,转变成低Ms值的γ′-Fe4N相和α-Fe(N)相,其中α-Fe(N)相的饱和磁化强度值与纯铁接近.
![]() |
图5 不同处理阶段试样的磁滞回线 Fig. 5 Hysteresis loop of samples with different treatment (a)—淬火; (b)—150℃回火,4.5h; (c)—150℃回火,13.5h. |
由含氮马氏体回火生成α″-Fe16N2相的过程为时效过程,在此过程中发生了α″-Fe16N2相的有序化转变.回火处理时,试样中首先生成柯氏气团,然后形成GP区.此时的GP区其实是一种无序化的α″-Fe16N2相.最后,延长保温时间或提高保温温度,GP区趋向于有序化,即形成了具有优异性能的α″-Fe16N2相.对于α″-Fe16N2相有序化过程,延长回火时间或提高回火温度有助于这一相变过程的发生,但是回火温度及时间均存在峰值.当对应实验参数超过峰值时,相变反应会向着时效反应的下一阶段进行,即α″-Fe16N2相分解生成α-Fe(N)相和γ′-Fe4N相.由此可知,回火温度及时间对α′-Fe(N)相向稳定相转变有促进作用.当这两项实验参数低于各自峰值时,回火反应处于促进α″-Fe16N2相生成的阶段;当高于对应峰值时,过高的能量使α″-Fe16N2相处于不稳定状态,诱发其发生分解反应转变为稳定相,生成α-Fe(N)相和γ′-Fe4N相.
本文中,回火温度和时间的峰值分别为150℃和4.5h.经过不同温度回火的样品中,150℃回火样品的α″-Fe16N2相析出量最高.虽然回火温度低于150℃时,样品中α″-Fe16N2相的析出量随回火温度的升高而增多,但当温度继续升高达到160℃时,样品中α″-Fe16N2相含量开始降低,样品中析出的α″-Fe16N2相开始发生分解反应.当温度升高到170℃时,α″-Fe16N2相消失.由于XRD无法检测质量分数低于5 % 的物相,所以当温度为160℃时,由于只有少量的α″-Fe16N2相发生分解,生成质量分数低于5 % 的γ′-Fe4N相,所以XRD图谱未出现γ′-Fe4N相衍射峰.对于不同的回火时间,当150℃回火样品的保温时间达到4.5h时,样品中α″-Fe16N2相的质量分数达到最高值50.57 % ,继续延长保温时间促进了样品中α″-Fe16N2相发生分解,样品中的α″-Fe16N2相质量分数降低.当保温时间增加到13.5h时,α″-Fe16N2相质量分数只剩下4.77 %.本文中140℃回火处理25.5h样品的回火保温时间虽然有明显延长,但其温度低于峰值150℃,样品中α″-Fe16N2相的质量分数为48.99 % ,低于150℃回火4.5h样品.
3 结 论1) 块状纯铁材料经过气固反应渗氮、退火、淬火及回火的过程,会获得α″-Fe16N2相含量较高的铁基磁性材料,其饱和磁极化强度高于220A · m2/kg.
2) 当回火温度在150℃,时间为4.5h时,氮化铁样品中α″-Fe16N2相的质量分数最高,达到50.57 % ,饱和磁极化强度达到223.6A · m2/kg,磁性能明显优于α-Fe(N)相和γ′-Fe4N相.
[1] | Kim T K,Takahashi M.New magnetic material having ultrahigh magnetic moment[J].Applied Physics Letters,1972,20(12):492-494.(![]() |
[2] | Komuro M,Kozono Y,Hanazono M,et al.Epitaxial growth and magnetic properties of Fe16N2 films with high saturation magnetic flux density[J].Journal of Applied Physics,1990,67(9):5126-5130.(![]() |
[3] | Nakajima K,Okamoto S.Large magnetization induced in single crystalline iron films by high-dose nitrogen implantation[J].Applied Physics Letter,1990,56(1):92-94. (![]() |
[4] | Takahashi M,Shoji H,Takahashi H,et al.Synthesis of Fe26N2 films by using reactive plasma[J].IEEE Transactions on Magnetics,1993,29(6):3040-3045.(![]() |
[5] | Gao C,Doyle W D,Shamsuzzoha M.Quantitative correlation of phase structure with the magnetic moment in RF sputtered Fe-N films[J].Journal of Applied Physics,1993,73(10):6579-6581.(![]() |
[6] | Liu W S,Tang J C,Du Y W.Nanocrystalline soft magnetic ribbon with α″-Fe16N2 nanocrystallites embedded in amorphous matrix[J].Journal of Magnetism and Magnetic Materials, 2008,320(21):2751-2754.(![]() |
[7] | Tang J C,Hong J M,Wu A H,et al.Saturation magnetostriction of α″-Fe16N2 phase[J].Journal of Alloys and Compound, 2009,479(1/2):32-34.(![]() |
[8] | Niizuma K,Utsushikawa Y.Formation of α″-Fe16N2 foil by nitrogen plasma irradiation[J].Vacuum,2004,73(3/4):499-503.(![]() |