2. 东北大学 材料与冶金学院, 辽宁 沈阳 110819
2.School of Materials & Metallurgy, Northeastern University, Shenyang 110819, China.
Corresponding author: LIU Chang-sheng, E-mail: csliu@mail.neu.edu.cn
在生产、加工和处理材料的过程中,由于材料局部区域产生不均匀的塑性变形,因而必然会产生残余应力.残余应力作为一种内应力对工件或材料各项性能的影响越来越受到人们的关注.目前检测残余应力的方法有很多种,作为一种新的应力检测手段,激光超声波检测法以其非接触、宽带、空间分辨率高等独特的优越性,近年来得到了快速的发展,成为国内外学者研究的热点[1, 2, 3, 4, 5, 6].由于声应力效应,当材料存在残余应力时,其弹性波传播速度将发生变化.因此可以根据所测声波速度的变化来反映其传播路径上的应力大小[7, 8].
本文主要应用有限元软件ABAQUS模拟了脉冲激光作用于薄板表面激发的表面波的传播过程,通过分析接收点的超声时域信号,得到了有残余应力和理想无应力状态下表面波的速度比,并与实验值和理论解进行对比分析[9],结果表明运用激光超声法对残余应力的检测有非常高的精度.
1 表面波的验证 1.1 建立ABAQUS有限元模型考虑1块各向同性均匀的薄板样品,材料为4140钢,屈服应力σS=930MPa,强度极限σb=1080MPa,其中y轴垂直于样品的表面,x轴和z轴分别垂直和平行于板边方向.假设脉冲线源激光沿着z轴辐照样品表面,平面xoy为各向同性平面,可以简化成平面应变问题来分析.建立有限元模型如图 1所示,长度L=13mm,厚度H=1.5mm,材料弹性模量E=199.5GPa,泊松比 μ=0.29,ρ=7858kg/m3.模型的下端和右端使用无限单元CINPE4消除来自边界的反射波干扰信号,约束左端x方向的位移.
![]() |
图1 ABAQUS有限元模型 Fig. 1 ABAQUS finite element model |
为了准确模拟脉冲激光对样品的作用,得到良好的表面波信号,如图 2所示,采用被调制过的高斯分布的脉冲载荷作为激励源作用在模型上表面,载荷作用点与光斑中心重合.有限元方法数值模拟激光超声问题时,为保证求解的精度和稳定性,需要选择合适的时间步长和单元长度.时间步长的选择主要根据求解的精度来确定.一般说来,时间步长应该足够小到能够反映激光作用样品的过程.时间步长越小求解精度越高,越能分辨出高频成分的超声波,但是也降低了计算效率.在这种情况下,需要考虑读取时间的准确性对时差法计算表面波速度的影响,本模型可选取时间步长 Δt=5×10-10s.一般情况下为精确模拟激光作用产生的弹性波的传播过程,要求网格尺寸小于弹性波波长的1/4.估算网格大小为0.042mm×0.0127mm,有限单元部分单元类型设置为CPE4,无限单元部分单元类型设置为CINPE4.使用ABAQUS里面的Standard分析步,采用固定增量步5×10-10s,脉冲激励的作用时间为5×10-7s,分析步的总时间为5×10-5s.
1.2 验证表面波的两个基本特性在模型表面取3个节点x1=7.065mm,x2=8.074mm,x3=9.041mm,输出每个节点的速度、位移的历程曲线,如图 3,图 4所示.比较图 3,图 4,可知节点1,2,3的速度、位移的幅值是一致的,符合表面波横向等值的基本特征.
![]() |
图2 高斯分布的脉冲 Fig. 2 Gaussian pulse |
![]() |
图3 节点1,2,3的速度-时间曲线 Fig. 3 The velocity-time curves of node 1,2,3 |
![]() |
图4 节点1,2,3的位移-时间曲线 Fig. 4 The displacement-time curves of node 1,2,3 |
沿y方向取3个节点y4=1.208mm,y5=1.335mm,y6=1.500mm,输出每个节点的速度、位移的历程曲线.
比较图 5,图 6,可知节点4,5,6的速度、位移的幅值随着深度的增加而逐渐衰减,符合瑞利表面波纵向递减的基本特征.因此,采用高斯分布的脉冲载荷来代替脉冲激光对样品的作用,可以得到信号良好的超声表面波.
![]() |
图5 节点4,5,6的速度-时间曲线 Fig. 5 The velocity-time curves of node 4,5,6 |
![]() |
图6 节点4,5,6的位移-时间曲线 Fig. 6 The displacement-time curves of node 4,5,6 |
应力对表面波波速的影响是十分微小的,100MPa的应力约改变千分之一的波速[10],为了精确地研究残余应力对表面波速度的影响,通过修改弹性模量的方法来引入应力场,引入修正的Bergman公式[9]:

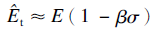

对于各向同性材料,Lame常数定义为
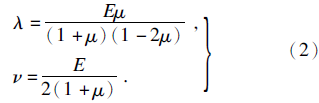
在ABAQUS软件的数值模拟中使用等效弹性模量来引入单向应力场,在弹性范围内,即σ≤σs,由公式
可得等效弹性模量与应力的关系见表 1.
![]() |
表1 等效弹性模量与应力关系 Table 1 The relationship between effective modulus and stress |
在模型表面依次取6个节点,x1=7.065mm,x2=8.074mm,x3=9.041mm,x4=10.009mm,x5=11.018mm,x6=12.027mm.与文献[9]中实验相符,为了避免激光光斑半径和测试点位置测量带来的误差,仍然采用逐差法计算瑞利表面波的速度.根据节点的时间-位移历程曲线得到每个节点位移达到最大值和最小值的时间tmax,tmin,计算表面波速度.
![]() |
图7 节点1,4的时间-位移曲线 Fig. 7 The displacement-time curves of node 1,4 |
由图 7可得

同理可得
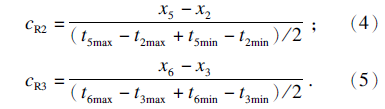
最后取平均值,得到该模型中的超声表面波速度:
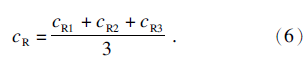
由公式(6)分别计算应力在0,230,461,691,807MPa下的表面波速度的有限元数值解;由公式(1)计算出表面波速度的理论值,比较分析表面波在有残余应力存在和理想无应力状态下的速度比的数值解、理论解和实验值.如图 8所示,表面波的波速随着应力的增加而减小,符合声弹性理论中应力与波速的定性关系[9].
![]() |
图8 表面波速度比的实验值、数值模拟值、理论值比较 Fig. 8 The surface wave velocity ratio comparison of experimental,calculated and theoretic values |
计算不同应力下表面波速度数值解与实验值的误差,如表 2所示,最大误差仅为0.024 % ,这表明该数值方法具有很高的精度,同时也说明应力对波速的影响很微小.
![]() |
表2 表面波速度比的数值解与实验值的误差 Table 2 The surface wave velocity ratio error of calculated and experimental values |
1) 用高斯分布的脉冲载荷来代替脉冲激光对样品的作用,同时引入无限单元来消除边界反射波的干扰信号,可以得到性能良好的超声表面波.
2) 采用修正的Bergman公式通过修改弹性 模量建立应力场,并计算不同应力状态下的表面波速的变化,得到了与实验结果吻合良好的数值结果.
[1] | Wang J J,Shi Y F,Lu L Z.Analysis of laser-generated ultrasonic force source at specimen surface and display of bulk wave in transversely isotropic plate by numerical method[J].Applied Surface Science,2012,258(6):1919-1923. (![]() |
[2] | Hess P,Lomonosov A M,Mayer A P.Laser-based linear and nonlinear guided elastic waves at surfaces (2D) and wedges (1D)[J].Ultrasonics,2014,54(1):39-55. (![]() |
[3] | Apetre N,Ruzzene M.Measurement of the Rayleigh wave polarization using 1D laser vibrometry[J].NDT & E International,2011,44(3):247-253. (![]() |
[4] | Duquennoy M,Ouaftouh M.Ultrasonic characterization of residual stresses in steel rods using a laser line source and piezoelectric transducers[J].NDT & E International,2001,34(5):355-362. (![]() |
[5] | Sanderson T,Ume C,Jarzynski J.Longitudinal wave generation in laser ultrasonics[J].Ultrasonics,1998,35(8):553-561. (![]() |
[6] | Mounier D,Poilane C,Khelfa H.Sub-gigahertz laser resonant ultrasound spectroscopy for the evaluation of elastic properties of micrometric fibers[J].Ultrasonics,2014,54(1):259-267. (![]() |
[7] | 沈中华,石一飞,袁玲,等.激光声表面波的若干应用研究进展[J].红外与激光工程,2007,36(sup1):240-244.(Shen Zhong-hua,Shi Yi-fei,Yuan Ling,et al.Progresses in the applications of laser induced surface acoustic waves [J].Infrared and Laser Engineering,2007,36(sup1):240-244.) (![]() |
[8] | Sanderson R M,Shen Y C.Measurement of residual stress using laser-generated ultrasound[J]. Pressure Vessels and Piping,2010,87(12):762-765. (![]() |
[9] | Nguyen T L.Development of an ultrasonic technique for the measurement of machining induced surface residual stresses[D].West Lafayette:Purdue University,2000. (![]() |
[10] | 潘永东,钱梦騄,徐卫疆,等.激光超声检测铝合金材料的残余应力分布[J].声学学报,2004,29(3):254-257.(Pan Yong-dong,Qian Meng-lu,Xu Wei-jiang,et al.Residual stress profiling of aluminum alloy by laser ultrasonics[J].Acta Acustica,2004,29(3):254-257.) (![]() |