Corresponding author: HUANG Feng, E-mail: hfork@163.com
出于环境保护和可持续发展的需求,材料加工领域的轻量化正成为研究热点.镁合金作为目前最轻的金属材料之一,由于具有较高的比强度和比刚度、良好的阻尼减震性能和电磁屏蔽效果,且零件尺寸稳定并易于回收,在航空、航天、汽车和3C产品等领域都具有广泛的应用前景[1, 2].传统的镁合金板带生产,由于加工工序长,不仅造成生产周期长和制造成本高的问题;由于加热工序多,严重的氧化还使制品的质量受到影响.薄带双辊铸轧技术作为材料加工领域内的前沿课题之一,以其短流程、低能耗的特点受到越来越多的重视.因此,将薄带双辊铸轧技术应用到镁合金板带制造中成为了近年来的一个研究热点[3, 4, 5, 6].
双辊铸轧是一个十分复杂的工艺过程,影响因素众多,再加上镁合金结晶潜热小、热传导性能好、高温下极易氧化的特性,使得镁合金薄带铸轧工艺参数可匹配的范围很窄[7, 8].如果只是采用实验方法,不仅耗时长、工作量大,还存在一定的盲目性.而通过计算机模拟计算可以方便地得到铸轧过程中各工艺参数对铸轧产品及铸轧工艺过程稳定性的影响规律.本文采用三维有限元软件ANSYS,对AZ31B镁合金立式连续铸轧凝固过程进行模拟,研究浇注温度及拉带速度等工艺参数对熔池内部金属流动及凝固特性的影响规律,以便更好地优化工艺,提高产品性能.
1 熔池内部传输控制方程在双辊铸轧过程中,由于在熔池内部同时存在液相区、固相区和两相区,为了简化模型,采用广义流体概念来统一处理这3个不同的相区[9].应用湍流模型,熔池内部的宏观传输控制方程可以用变量φ统一表示为
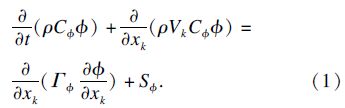
统一方程中各项的表达式如表 1所示.gx,gy,gz分别为重力加速度在3个方向上的分量;μeff和Keff分别为有效黏度系数和有效导热系数.
![]() |
表1 控制方程中各项的表达式 Table 1 Components of general governing equation |
1) 水口入口区域:

2) 熔池自由表面.熔池表面在y方向的速度为零,所有变量在y方向上的梯度为零,同时熔池表面与熔池上方的保护气体间进行热辐射换热:
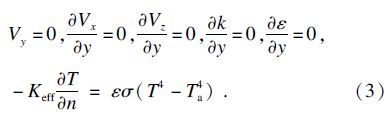
3) 中心对称面:

4) 轴向对称面:

5) 熔池与侧封板的接触侧面:

侧封板作为保温材料导热性能不好,可以认为其温度为恒定值,由于经过预先加热,本研究中取为600℃.
6) 移动边界:认为铸辊和凝壳之间无滑动,因此边界上节点速度即为铸辊的线速度:

熔池与铸辊表面间的传热视为第三类热边界条件:

7) 黏度系数的处理:当温度为200,566,590,632,650和680℃时,黏度分别为105,105,0.012,0.00127,0.00124和0.00120kg · m-1 · s-1.
8) 凝固潜热的处理:采用等价比热容方法处理凝固潜热,假设凝固潜热在凝固区间内均匀释放,且固相率与温度成线性关系,则镁合金的比热可表示为
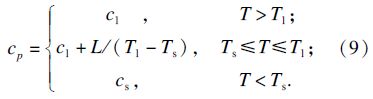
数值模拟采用大型商业有限元软件ANSYS进行运算,考虑到水口及熔池的对称性,采用熔池的1 /4作为模拟区域,如图 1所示.由于模拟区域的上下部分尺寸差异很大,因此采用了智能网格划分方法,相比于均匀网格划分,避免了熔池上下部分网格尺寸的过大差异,同时显著降低了单元数量,在保证模拟结果精度的同时,还大幅提高了计算效率.
![]() |
图1 计算区域的网格划分 Fig. 1 Mesh of computing region |
模拟的具体条件:铸辊直径为500mm,辊身长为250mm,铸带厚度为2mm,熔池液面高度控制在160mm;浇注温度分别为640,650,660和670℃,铸轧速度分别为15,20,25和30m/min.铸轧材料为镁合金AZ31B,具体物性参数如表 2所示.
![]() |
表2 AZ31B镁合金的热物性值 Table 2 Thermophysical properties of AZ31B magnesium alloy |
在铸辊的转速为25m/min,浇注温度分别为640 ,650,660 和670 ℃时,熔池中心对称面的温度场如图 2所示.由图 2可以看出,在其他工艺条件不变的情况下,随着浇注温度的增加,即过热度的增大,熔池内部两相区的区域扩大,凝固终了点的位置向出口方向移动.当浇注温度提升到670℃时,在出口处铸带芯部温度已经高于固相线,此时铸带容易拉断,造成漏液事故.过高的浇注温度也会造成铸带及熔池表面的氧化,所以在此条件下合适的浇注温度应控制在660℃以下.
![]() |
图2 不同浇注温度下中心对称面的温度分布 Fig. 2 Temperature distribution of centrosymmetric area under different pouring temperature (a)—640℃; (b)—650℃; (c)—660℃; (d)—670℃. |
在浇注温度为650℃,铸轧速度分别为15,20,25和30m/min时 ,熔池中心对称面的温度场如图 3所示.可以看到在此条件下,熔池内部的温度分布对铸速非常敏感,随着铸轧速度的提高,凝固终了点大幅向出口方向移动.
![]() |
图3 不同铸轧速度下中心对称面的温度分布 Fig. 3 Temperature distribution of centrosymmetric area under different casting speed (a)—15m/min; (b)—20m/min; (c)—25m/min; (d)—30m/min. |
在铸速为15m/min时,由于凝固终了点位置靠上,凝固壳过厚,导致铸轧力过大,不仅容易出现裂纹等缺陷,还容易造成轧卡事故.当铸速达到30m/min时,凝固终了点已经接近到了熔池的出口处,此时铸带中心容易出现液芯,造成断带事故.在此浇注温度下,适宜的铸速应控制在20~30m/min之间.
浇注温度为650℃时,不同铸轧速度下熔池轴对称面的流场分布如图 4所示.由于浇口采用侧面开口的方式,镁合金熔液以一定的角度和速度流向侧封板,然后再回流到熔池中心部分.由图 4可以看出,随着铸速的提高,从侧封板回流的趋势加强,在熔池的上下部分形成的漩涡也愈加明显,热量随着流动传输,不仅造成了熔池内部温度的提升,同时也能有效减小熔池边部与熔池中心的温度差.
![]() |
图4 不同铸轧速度下轴对称面的流场分布 Fig. 4 Flow field of axisymmetric area under different casting speed (a)—15m/min;(b)—20m/min;(c)—25m/min;(d)—30m/min. |
1) 应用广义流体的思想,建立了适用于立式双辊铸轧过程熔池内部的宏观传输统一控制方程,并采用智能网格划分技术,应用有限元方法,成功实现了对镁合金铸轧过程熔池内部的热-流耦合模拟.
2) 随着浇注温度的增加,凝固终了点位置向熔池出口处移动.
3) 铸轧速度对熔池内温度分布影响显著,凝固终了点位置随铸速的提高明显向铸带出口移动.
4) AZ31B镁合金薄带双辊铸轧合适的工艺参数为浇注温度640~660℃,铸轧速度20~30m/min.
[1] | Mordike B L,Ebert T.Magnesium properties-applications-potential[J].Materials Science and Engineering A,2001,302:37-45.(![]() |
[2] | 余琨,黎文献,王日初,等.变形镁合金研究、进展及应用[J].中国有色金属学报,2003,13(2):277-287. (Yu Kun,Li Wen-xian,Wang Ri-chu,et al.Research,development and application of wrought magnesium alloy[J].Chinese Journal of Nonferrous Metals,2003,13(2):277-287.)(![]() |
[3] | 王广山,邸洪双,黄锋.双辊铸轧镁合金薄带冷轧实验研究[J].东北大学学报:自然科学版,2009,30(6):825-828. (Wang Guang-shan,Di Hong-shuang,Huang Feng.On the cold rolling of twin-roll casting magnesium alloy strip [J].Journal of Northeastern University:Natural Science,2009,30(6):825-828.)(![]() |
[4] | Liang D,Cowley C B.The twin-roll strip casting of magnesium alloys[J].Journal of the Minerals,Metal & Materials Society,2004,56(5):26-28.(![]() |
[5] | Park S S,Lee J G,Park Y S,et al.Fabrication of Mg alloy strips by strip casting[J].Materials Science Forum,2003,419:509-514.(![]() |
[6] | Watari H,Koga N,Paisarn R.Formability of magnesium alloy sheets manufactured by semi-solid roll strip casting[J].Materials Science Forum,2004,449:181-184.(![]() |
[7] | Watari H,Haga T,Koga N,et al.Feasibility study of twin roll casting process for magnesium alloys[J].Journal of Materials Processing Technology,2007,192/193:300-305.(![]() |
[8] | Ju D Y,Hu X D.Effect of casting parameters and deformationon microstructure evolution of twin-roll casting magnesium alloy AZ31[J].Transactions of Nonferrous Metals Society of China ,2006,16:874-877.(![]() |
[9] | 苗雨川,邸洪双,张晓明,等.不锈钢薄带铸轧过程中的流动特性[J].钢铁研究学报,2000,12(4):14-18. (Miao Yu-chuan,Di Hong-shuang,Zhang Xiao-ming,et al.Flow field of stainless strip during roll-casting[J].Journal of Iron and Steel Research,2000,12(4):14-18.)(![]() |