随着高炉大型化和高压化,高炉日生产铁可达到万吨以上[1, 2].高炉冶炼中有大量高温液态的生铁和炉渣由高炉下部的出铁口放出.铁水从高炉出铁口流入主铁沟,经过撇渣器,到达支铁沟后流入铁水罐.目前大型高压高炉出铁口距离地面高度7~9 m,铁沟长度可达40~50 m,宽度最大为1.2 m.可见从高炉出铁口中射出的铁水具有一定的初动能,且出铁沟有一定的坡度.
目前钢铁行业广泛使用由日本新日铁提出的KR搅拌法脱硫技术,它是将搅拌器浸入铁水罐内旋转搅拌,同时加入脱硫剂使其卷入铁水内部从而达到铁水脱硫的目的[3, 4].但对冶金反应器内搅拌高温(1 500 ℃以上)熔体的搅拌器叶轮的材料强度要求太高,而且这些易损的叶轮残渣混入钢液中,造成钢液的二次污染.德国的ATH法(斜插喷枪)和日本新日铁的TDS法(顶喷)提出了喷吹法脱硫的方法[5, 6, 7].喷吹法用载气将脱硫剂经喷枪吹入铁水深部,使粉剂与铁水充分接触,在上浮过程中将硫去除.也有采用钟罩插入法脱硫的方法[5].另外,铁水炉外脱硫也有采用机械、气体复合搅拌的脱硫方法[8, 9].日本学者丸川等[2]提出,把从若干座高炉出来的成分不同的铁水集中起来流进漏斗型反应器,利用铁水出流的动能和势能在漏斗型反应器内形成旋流,从而实现脱硫脱磷等冶炼功能.现有铁水预处理方法存在着诸如喷溅严重、喷枪污染、铁耗大、脱硫剂利用率低、温降大等诸多问题,因此有必要进行工艺优化或开发更环保和易操作的工艺.本文提出在铁水沟处建立脱硫坑,利用出铁沟中铁水重力势能搅拌铁水、脱硫的方法.脱硫效率主要由喷射参数和处理容器内脱硫粉剂与铁水的混合程度来决定,因此,研究反应器的搅拌特性和粉剂在铁水内的停留时间分布或平均停留时间,以及粉剂与铁水的均匀混合时间等参数很重要.
本文建立了高炉出铁重力势能脱硫冶金反应器的数值模型,对反应器的搅拌特性及铁水停留时间分布等进行了模拟研究,并与实验结果作对比.在所得流场结果的基础上对夹杂物行为和液面波动等进行了初步分析.研究证实,这种新型重力势能驱动反应器能够产生高强度稳定的旋流,对进一步改进其反应器脱硫效率具有重要意义.
1 数学模型为了研究反应器内流体流动的规律,本文用到连续性方程(式(1))和动量方程(式(2)):
钢液和空气的两相流动行为采用多相流动体积法(VOF)求解.对于多相流动问题,引入每相的体积分数,所有相的体积分数之和为1,即φgas+φsteel=1,式中φgas,φsteel分别为空气和钢液的体积分数.密度表达式为ρ=φgasρgas+φsteelρsteel,其中,ρgas和ρsteel分别为空气和钢液的密度.自由液面运动轨迹的跟踪是通过计算网格同时求解每单位体内流体体积分数来实现的.液气界面的跟踪通过求解连续方程<来完成.式中vi为速度分量,xi为坐标分量,i=1,2,3.
反应器内铁水的混合特性根据在反应器入口处加入的示踪剂瞬态扩散过程进行计算,示踪剂的传输方程为
旋流反应器内夹杂物的运动和分布情况采用DPM离散项模型.离散相夹杂物颗粒的作用力平衡方程通过积分拉氏坐标系下的颗粒作用力微分方程来求解,即颗粒惯性等于作用在颗粒上的各种力:
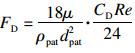
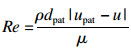

碗型反应器结构和网格如图 1所示.本工作采用FLUENT软件模拟反应器的流场、夹杂物粒子轨迹和示踪剂浓度等.
![]() | 图 1 碗型反应器结构示意图和网格划分示意图 Fig. 1 Schematics of structure and grids used for simulation of the bowl-shape reactor |
空间离散采用二阶迎风格式,控制方程采用二阶隐式分离求解器,流体的压力-速度修正选择PISO算法.为了考虑流场的速度梯度对夹杂物的影响以及湍流漩涡对颗粒运动轨迹的影响,在DPM离散相模型中选择了Saffman升力和随机游走模型.利用DELL T610服务器并行计算,时间步长设置为10-3s.
反应器的入口边界条件设定为:速度入口Velocity-inlet,相对应的湍动能和湍动能耗散率分别为k=0.01v2和ε=k1.5/0.04;速度出口Outlet 对应的边界条件为Outflow;墙壁采用标准壁面函数,设置成无滑移光滑壁面.DPM离散项模型中设粒子数为30个,其速度方向和大小与进口速度相同.对于夹杂物,设为escape 边界,夹杂物到达出口时从出口逃逸.
3 结果与讨论图 2所示为碗型反应器典型水平截面的速度场和湍动能场分布.由图可以看出,铁水从入口流入后,受惯性力作用出流以近似于切线的方向碰撞到圆形侧壁.旋流是在射流碰撞到离心室壁面的影响下形成的,由于侧壁的黏滞作用,旋流强度逐渐衰减;当铁水到达反应器底部时,速度已减少为初速度的一半以上,并且漩涡的中心向水口方向偏离,这是由于水口位置的偏心造成的.图 3所示为碗型、圆台型和圆锥型等3种不同结构反应器内典型主截面的速度场分布和等值线分布.可以看出这3种反应器内液体的旋流效果很明显,从等值线图可以清楚地看出碗型反应器内速度梯度是最小的,说明这时旋流的衰减是最慢的,有利于脱硫粉剂与铁水的混合,达到有效脱硫的目的.
![]() | 图 2 碗型反应器内典型水平截面的速度场和湍动能场分布(T=40 s, v=0.69 m/s) Fig. 2 Velocity vectors and turbulence kinetic energy contours on horizontal sections in bowl-shape reactor(a)—入口水口截面y=0.18 m; (b)—中间截面y=0.1 m; (c)—出口水口截面y=0.025 m. |
![]() | 图 3 典型截面的速度场和等值线分布(T=40 s) Fig. 3 Velocity vectors and isolines on typical sections(a)—碗型; (b)—圆台型; (c)—圆锥型. |
图 4所示为3种典型水平截面沿x轴方向的速度分布.y=0.15 m为通过入口的平面,由于入口射流的影响,旋流速度达到最大值.随着离反应器底部的距离逐渐缩小,反应器内的速度呈线性下降,这是由于壁面的剪切力对液面起阻碍的作用,使旋流速度不断降低.图 5所示为3种结构反应器内底部靠近出口处的湍动能值随时间的变化曲线.可以看出,当流动达到稳定时,碗型结构反应器靠近出口处的湍动能要明显小于其他两种结构.这说明碗型结构反应器流体的动量损失更大,流体的速度更小,流体在反应器内停留的时间更长,更有利于脱硫粉剂和铁水的混合.
![]() | 图 4 沿x轴方向的速度分布(T=40 s) Fig. 4 Velocity distribution along x axis |
![]() | 图 5 出口处湍动能随时间的变化 Fig. 5 Variation of turbulence kinetic energy with time |
根据冶金反应工程学理论,冶金反应器内的流动状态可依据示踪剂变化曲线来分析.本文的反应器流场特性可以用进入反应器内的示踪剂浓度变化来分析.在入口处,示踪剂浓度相当于输入一个脉冲信号,而反应器出口输出的示踪剂浓度曲线因流场分布不同而变化.图 6所示为通过水模型实验和数值模拟获得的反应器内不同时刻示踪剂浓度随时间的变化情况,两者浓度扩散趋势基本吻合.初始时间为40 s.可以看出,当示踪剂从入口流入后,由于反应器的流体处于旋流,示踪剂沿着反应器侧壁流体流动.当示踪剂沿侧壁流动旋转达到一圈时,由于不断的扩散,示踪剂已经占据反应器的一半.
![]() | 图 6 不同时刻反应器内流场分布 Fig. 6 Flow fields of reactor at different moments |
当在碗型反应器入口处注入示踪剂时,反应器出口处示踪剂浓度随时间的变化如图 7所示,具体的实验方法和死区体积分数、活塞流和全混流体积分数等参数的定义可参考文献[10].从图中可以看出,浓度曲线出现了双峰,这说明反应器内出现了二次流.对RTD数据进行分析处理,得到了反应器内液体混合特性的定量结果,见表 1.从表中可以看出,数值模拟与水模实测的结果较为接近,反映了反应器内钢液的流动特征,两者的一致性进一步验证了数值模拟结果的可靠性.
![]() | 图 7 数值模拟和水模型实验得到的质量浓度曲线 Fig. 7 Concentration curves of numerical simulation and physical experiment |
![]() | 表 1 RTD曲线分析结果Table 1 Results of RTD analysis |
图 8所示为3种结构反应器内粒子的运动轨迹.由图可知:粒子在进入反应器后沿着侧壁流动,由于初速度比较大,因此粒子会在大约旋转一周时,沿螺旋线轨迹旋转向下流动;当粒子正好旋转到底部出口时,则会从出口流出,否则粒子继续沿螺旋线旋转,直到最后流出反应器,这与浓度曲线计算得到的结果相符合.
![]() | 图 8 三种结构反应器内粒子运动轨迹 Fig. 8 Trajectories of tracer particles in three types of reactor |
图 9为不同反应器入口流速条件下计算得到的反应器铁水-空气界面波动形态图.由图可见,随着入口的流速从0.669 m/s 增大到1.2 m/s,自由液面的波动范围从0.006 m增大到0.015 m.随着入口初速度不断增大,液面中出现凹面的位置离水口距离越来越远.
![]() | 图 9 三种结构反应器液面波动形态 Fig. 9 Surface fluctuation in three types of reactor |
1) 以金属液自身重力势能作为金属冶炼搅拌动力的冶金反应器,无需外加能源和动力完成铁水的脱硫过程,降低环境负荷,保护地球环境.
2) 碗型结构反应器底部靠近出口处湍动能明显小于其他两种结构.这说明碗型结构反应器流体的动量损失越大,流体的速度越小,流体在反应器内停留的时间越长,越有利于脱硫粉剂和铁水的混合.
3) 粒子进入反应器后沿着侧壁流动,大约旋转一周时,沿螺旋线轨迹旋转向下流动,当粒子正好旋转到底部出口时,则会从出口流出;否则粒子继续沿螺旋线旋转,直到最后流出反应器.
[1] | Shigeru U,Shungo N,Hiroshi N,et al.Recent progress and future perspective on mathematical modeling of blast furnace[J].ISIJ International,2010,50(7):914-923.(![]() |
[2] | Kurunov I F.The direct production of iron and alternatives to the blast furnace in iron metallurgy for the 21st century[J].Metallurgist, 2010,54(5):335-342.(![]() |
[3] | Kiyoshi S,Syozo K,Akimitsu K,et al.Sequential dephosphorization and desulphurization of hot metal by newly developed pretreatment furnace[J].The Iron and Steel Institute of Japan, 1987,73(11):1567-1574.(![]() |
[4] | Amit C.Ironmaking in conventional and mini blast furnaces.part I:the conventional blast furnace[J].Steel Times International, 2006,30(8):48-52.(![]() |
[5] | Freissmuth A.Desulphurization of hot metal by using calcium carbide—the present situation and possible developments[J].Stahl und Eisen,1997,117(9):53-59.(![]() |
[6] | Sandberg H.Desulphurization of hot metal[J].Ironmaking and Steelmaking,1977,4(5):280-284.(![]() |
[7] | Zou Z S,Zou Y S,Zhang L B,et al.Mathematical model of hot metal desulphurization by powder injection[J].ISIJ International, 2001,41(sup):66-69.(![]() |
[8] | Kijac J,Borgon M.Desulphurization of steel and pig iron[J].Metalurgija,2008,47(4):347-350.(![]() |
[9] | Fazel Z M H,Türks,en I B,Torabi K O.Type-2 fuzzy modeling for desulphurization of steel process original research article[J].Expert Systems with Applications, 2007,32(1):157-171.(![]() |
[10] | 王芳.移动磁场作用下钢液湍流的大涡模拟及气液两相流行为的研究[D].沈阳:东北大学,2009.(Wang Fang.Large eddy simulation on turbulence of molten steel and behavior of gas /liquid two phase flow affected by alternative magnetic field[D].Shenyang:Northeastern University,2009.)(![]() |