2. 双鸭山建龙矿业有限公司, 黑龙江 双鸭山155126
2. Shuangyashan Mining Company of Jianlong Iron & Steel Group Co., Ltd., Shuangyashan 155126, China.
Corresponding author: MA Jiao-yang, E-mail: mjy20006@126.com
急倾斜破碎中厚矿体是当今矿业难采矿体之一,其倾角、厚度决定了回采进路需要沿脉布置,利于分段高度取较大值,但其破碎性使得切割工程形成难度增大,此外,沿脉巷道如何才能保障服务期内安全稳固成为一大问题;若降低分段高度,其采准工程量将增大,加之我国此类条件的矿山,大多数属于品位较低的矿山,无形中增大了开采成本,严重降低矿石回收率.为此,需要研究更适合此类矿体条件的采矿方法.近年来,诱导冒落法作为一种新型采矿方法,以工艺简单、成本低、安全等优点,在和睦山铁矿倾斜、矿体与下盘近矿围岩极不稳固、上盘围岩较稳固的厚大矿体中首次成功应用,解决了软破矿岩地压控制与高强度回采等难题.基于此,本文依据双鸭山矿体条件,试验性地将诱导冒落法改进应用,以期解决这一难采问题.
1 双鸭山铁矿北区开采条件双鸭山铁矿北区矿体为磁铁石英岩和赤铁石英岩,以磁铁矿为主,呈层状产出,走向长约3000m,厚度3~12m,平均厚度约10m,倾角63°~90°,为急倾斜中厚矿体,矿石节理裂隙发育稳固性较差,部分破碎区段极不稳固.上盘为石榴云母石英片岩、矽线石榴斜长片麻岩、含铁石英片岩、含铁石英片麻岩等,大多数区段中等稳固,部分区段稳固性差.下盘为有轻微矽化的透辉石大理岩、矽线石榴斜长片麻岩、云母石英片岩和含铁石英片岩,整体情况中等稳固.矿山应用浅孔留矿法与阶段矿房法开采,在第1~12勘探线之间的620m长范围,矿体与上盘破碎,采准、切割工程均难以形成,即使强支护形成后,也难以维持到服务期,采场安全条件极差;出矿效率低;矿石损失、贫化大,使这两类采矿方法受到不同程度的制约.为此,本文提出诱导冒落法开采方案.
2 诱导冒落法方案 2.1 诱导冒落工程布置方式针对双鸭山北区矿体条件,采用沿脉进路布置诱导冒落法方案(见图 1),即沿矿体下盘布置沿脉进路,回采时爆破出足够宽度的拉底空间,诱导上部矿石自然冒落,诱导冒落区的矿石从进路端口放出一部分,剩余部分在下分段回采时回收.
![]() | 图 1 诱导冒落法开采方案 Fig. 1 The mining scheme of induced caving method 1—沿脉出矿进路;2—出矿横穿;3—出矿联巷;4—落矿炮孔;5—覆岩;6—上分段残留矿体;7—炮孔推进方向;8—切割巷道;9—矿体界线;α—矿体倾角;H—阶段高度;h—崩落高度;L—采场长度;A—诱导冒落区;B—崩落区. |
选择倾角α≥75°、厚度大于8m的中厚破碎矿体实施此方案;通过现场调研,在矿岩稳固性分析基础上,根据力系平衡原理得出矿体临界跨度不超过24m,其跨度值小于顶板围岩的最小临界跨度38m[1],即诱导冒落区矿石先于围岩冒落于崩落区(出矿后形成的空区内),伴随跨度不断增大,采场内存在的部分散体矿石对围岩有支撑作用,空区跨度达不到诱导顶板围岩自然冒落的尺度,保障上、下盘岩石不掺入矿石流;将穿脉间距取100m,分段高度50m,进路位置靠近下盘布置.
2.1.2 切割方式矿石不稳固,切割天井难以形成,因此,采用切割巷+斜排炮孔的拉槽方法,利用切割巷道作为补偿空间,在采场的中间拉开切割槽,即在回采进路中钻凿8排角度逐渐增大的扇形炮孔,分三次微差爆破(前两排一次,剩余炮孔三排一次)形成切割槽:待一次爆破完成后,由回采进路回收崩落的矿石,之后进行第二、三次爆破.上、下分段切割工程交错布置,以利于上分段诱导冒落的矿石得到很好的回收.
2.1.3 回采工作采用中间开切割向两端退采的回采方式.不同的倾角诱导上部矿体的难易程度不同[2, 3],根据现场调研情况分析:矿体倾角越大,冒落拱扩展方向越容易控制,诱导冒落高度可取较大值,此外,应保障诱导冒落的矿石有足够的空间可以容纳,因此,试验采场中矿体倾角α>85°,预先设计崩落区炮孔深度25m,诱导冒落区冒落高度约25m;当矿体倾角75°≤α≤85°时,预先设计崩落区炮孔深度30m,诱导冒落高度20m.在满足临界冒落跨度的条件下,为形成足够宽度的崩落空间,将上盘侧炮孔最好不设计到矿体边界,防止上盘岩石过早冒落与混入;下盘边孔角布置在有效爆破范围内,应尽可能使更多诱导冒落区矿石处在预测冒落线之内,且应崩落适当(尽可能少)的下盘岩石,因此,下盘边孔角最小不能低于55°,且边部布置3个炮孔,促使诱导区矿体顺利冒落.炮孔排距的大小根据爆破夹制力和炮孔爆破的方向性确定,在矿体水平厚度8~15m的范围内,炮孔排距采用2~2.5m为宜,每排炮孔的个数根据矿体厚度而定[4].凿岩设备选用QJZ-100B潜孔钻机,孔径90mm,出矿设备选用Z-30AW装岩机.
2.1.4 安全保障沿脉出矿进路采用半圆拱断面形状、简易光面爆破、喷锚网联合支护的方式.考虑到爆破震动与地压活动影响,锚杆应紧跟工作面支护,采用初始力较大的水泥卷锚杆,锚杆长度2.0m左右为宜,视围岩的破碎程度取排距0.8~1.0m、排内间距0.7~1.0m,每掘进2~3个循环,喷射混凝土封闭围岩.考虑到诱导冒落区矿石冒落过程中,绝大多数矿石将会撞击下盘围岩,减小了冒落过程大块产生的空气气浪冲击,因此,可通过式(1)求得所需安全垫层的最小厚度[5].北区矿体预留厚度3~3.5m垫层可保证回采工作安全,按量控制放出,放出崩矿量的80%左右,保证出矿口上方留下不小于3m的矿石散体垫层.

开挖方式不同,应力分布状态不同,冒落的形式也就不同.由采场中部开切割向两边退采方式,诱导冒落区矿石冒落[6, 7, 8]过程可分析如下:(1)诱导冒落区矿体起初是稳固的块体,没有明显冒落迹象;(2)当冒落跨度达到临界冒落值时,开始零星冒落;(3)伴随跨度增大,进入持续冒落阶段;(4)拱面中心部分诱导冒落区矿体高度越来越小,拱顶塌透,此时,诱导冒落区矿体形成类导流[9]放矿条件,有利于上部残留体的回收;(5)诱导冒落区矿体侧向崩落并逐渐变小、失稳,当开挖达到两横穿时,诱导冒落矿体几乎完全下落.
冒落块度大小与节理发育程度、受力状态及爆破震动效应关系密切.双鸭山矿岩点荷载强度皆小于7MPa,节理发育,矿岩破碎;随着开采深度的增加,地应力危害越来越严重,而这些应力在诱导冒落中起积极作用,促进诱导冒落区矿石下落;采用沿切割向两边退采的方式,爆破震动呈左右相互影响状态,有利于诱导冒落区矿体裂纹进一步发育[10].此外,诱导冒落区上分段没有回收的冒落矿块会伴随下分段放矿过程,通过冲击、碰撞、挤压变得更破碎.
2.3 崩矿损失、贫化预计采矿过程中的损失、贫化是衡量采矿方法合理程度的重要指标,根据冒落规律,诱导冒落工程中引起损失、贫化的区域见图 2.
![]() | 图 2 诱导冒落工程中的损失区、贫化区 Fig. 2 The loss and dilution zone of the induced caving project 1—沿脉出矿进路;2—出矿横穿;3—出矿联巷;4—落矿炮孔;5—冒落线;6—引起贫化区域;7—引起损失区域; H—阶段高度,m;W—矿体厚度,m;h—崩落区高度,m; l—进路高度,m;α—矿体倾角,(°);β—边孔角,(°); A—诱导冒落区;B—崩落区. |
根据矿体形态,诱导冒落试验采场结构参数对损失、贫化进行了整合推算.将回采进路布置在紧靠下盘的矿体内部,即进路位置不变,而倾角、厚度、崩落区高度等参数都是在一定范围内的变化值,为此,整理计算得到该方案布置下的损失率、贫化率,见式(2),式(3).
损失矿石量:Rs=ρ矿石Llλsinβ;
贫化矿石量:
Rp=ρ岩石L(H-h)[(H-l)cotα-λcosα];
采出矿石量: Qc=2HLWρ矿石;
预估贫化率:
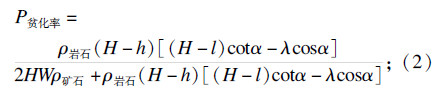
预估损失率:

S5试验采场:进路尺寸为宽×高=2.8m×2.8m,边孔角取值为60°,诱导冒落高度为25m,倾角约为85°,矿体平均厚度约为9m时,崩矿引起的贫化率为2.63%,损失率为8.79%.
3 诱导冒落试验采场情况为了检验诱导冒落参数的合理性,在S5号采场做了现场试验.S5号采场回采初期,爆破了5排炮孔,设计崩落矿量13920.5t,实际出矿量 13348.7t,回收率为95.9%,且冒落块度良好,几乎不需要二次破碎,与分析情况基本吻合;随着回采的进行,当次炮排爆破后矿石的回收率达到128.2%,说明回收了部分诱导冒落区矿石.诱导区顶板冒透后,采场内明显有混岩迹象,此时,对S5采场出矿过程中混岩情况和最大矿石块度(见表 1)进行了跟班标定(见图 3).
![]() | 图 3 第1067车时沿脉进路放矿口散体特征 Fig. 3 The granular media characteristics of following-vein drift of No.1067 car |
![]() | 表 1 S5号采场跟班统计 Table 1 The regular shift recordings of No.S5 stope |
结果显示:随着回采的进行,其废石混入量呈交替上升趋势变化.根据混岩情况的变化及现场跟踪出矿情况判断,废石混入的变化主要由两方 面因素影响:其一,爆破块度的影响,爆破后采场内矿岩块度较正常情况明显高出许多,最大块度尺寸达1.4m×0.6m×0.5m;其二,诱导冒落后期施工中,凿岩巷道相对靠近矿体上盘,对爆破效果造成影响,使得冒落拱扩展方向沿上盘拓展,影响矿石回收.在以上两因素影响下,采场内矿岩在流动过程中大块经常堵塞上盘侧放矿口,在大块堵塞期间,下盘侧矿石流出较多,混岩量变小;伴随出矿量的逐渐增多,当采场上盘侧堵塞大块从采场内流出时,上盘岩石也随之流出,混岩量明显上升;伴随出矿的进行,当采场上盘侧再次被大块堵塞时,从而出现新一轮的混岩量突然变小,后逐渐增大的现象.但总体上回收指标较好,而诱导冒落后期产生的混岩率问题,可通过合理优化凿岩巷道位置,保障爆破效果得到解决.
4 结 论1) 确定了实施诱导冒落法的矿体条件(倾角α≥75°、厚度大于8m的中厚破碎矿体),采用切割巷+斜排炮孔的拉槽方法,中间开切割向两端退采的回采方式,上、下分段切割工程交错布置,可解决切割工程难以形成,诱导区矿石滞留崩落区等问题.
2) 为了控制冒落拱扩展方向,且保障诱导冒落的矿石有足够的空间可以容纳,给出不同倾角的诱导冒落区高度,矿体倾角α>85°时,诱导冒落区矿体的高度取为25m;矿体倾角75°≤α≤85°,诱导冒落区矿体的高度取20m.防止上盘岩石过早冒落与混入,促使诱导区矿体顺利冒落,上盘侧炮孔最好不设计到边界,下盘边孔角布置在有效爆破范围内;采用联合支护,预留矿石垫层3~3.5m,保障采场安全回收.这种布置下,可有效控制诱导冒落区的冒落进程及冒落块度.
3) 根据矿体条件和诱导冒落参数关系,给出不同矿体倾角、厚度、边孔角、进路高度、崩落区高度与损失、贫化之间的关系式,并计算了矿体倾角85°时,崩矿的损失率为8.79%,贫化率为2.63%,进一步验证了诱导冒落工程布置的合理性.
4) 从现场试验反馈情况对诱导冒落参数进行检验,结果表明:回采初期,回收率较高,冒落块度良好,与分析情况基本吻合;诱导区顶板冒透后,混岩量呈交替上升趋势变化.总体回收指标较好,诱导冒落后期产生的混岩问题可通过合理优化凿岩巷道位置,保障爆破效果得到解决.
[1] | 常帅.双鸭山铁矿北区采矿方法研究[D].沈阳:东北大学,2008.(![]() |
[2] | Zhang Z X,Xu Y,Kulatilake P H S W,et al.Physical model test and numerical analysis on the behavior of stratified rock masses during underground excavation[J].International Journal of Rock Mechanics & Mining Sciences,2012,49(1):134-147.(![]() |
[3] | Wei X J,Gao M Z,Lyu Y C,et al.Evolution of a mining induced fracture network in the overburden strata of an inclined coal seam[J].International Journal of Mining Science and Technology,2012,22(6):779-783.(![]() |
[4] | Ren F Y,Sow T A M,He R X,et al.Optimization and application of blasting parameters based on the “pushing-wall” mechanism[J].International Journal of Minerals,2012,19(10):879-885.(![]() |
[5] | 曹建立,任凤玉.诱导冒落法处理时采空区散体垫层的安全厚度[J].金属矿山,2013,43(3):45-48.(![]() |
[6] | Shabanimashcool M,Li C C.Numerical modelling of longwall mining and stability analysis of the gates in a coal mine[J].International Journal of Rock Mechanics & Mining Sciences,2012,51:24-34.(![]() |
[7] | Jiránková E,Petroš V,Šancer J.The assessment of stress in an exploited rock mass based on the disturbance of the rigid overlying strata[J].International Journal of Rock Mechanics & Mining Sciences,2012,50:77-82.(![]() |
[8] | Xu X L,Zhang N,Tian S C.Mining-induced movement properties and fissure time-space evolution law in overlying strata[J].International Journal of Mining Science and Technology,2012,22(6):817-820.(![]() |
[9] | 曹建立,任凤玉,张晋军,等.分段卸压崩落法导流放矿实验研究[J].东北大学学报(自然科学版),2011,32(8):1186-1189.(![]() |
[10] | Zhou C B,Yao Y K,Guo L W,et al.Numerical simulation of independent advance of ore breaking in the non-pillar sublevel caving method[J].Journal of China University of Mining and Technology,2007,17(2):295-300.(![]() |