氢在一定程度上能溶解于铝熔体.氢在液态铝的溶解度是在固态铝中溶解度的20倍[1].氢是引起铝合金气孔和疏松的主要原因[1, 2].疏松和气孔一旦在凝固过程中形成就很难在后续的塑性变形和热处理过程中去除[3, 4],因此在铸造之前要对铝合金熔体进行净化处理.铝合金除气方法主要有:熔剂法[1]、旋转除气法[5, 6, 7]、真空除气法[8, 9, 10]、超声振动除气法、转子-定子强剪切除气法、熔剂超声联动除气法等.目前旋转除气法是应用最为广泛的方法.旋转除气法通过一定形状的转子向熔体中通入惰性气体或活性气体,并依靠转子的高速旋转来打碎气泡,气泡在上浮过程中,利用分压差原理和吸附原理将氢和固态夹杂物带出熔体液面,从而达到净化效果.
尽管目前旋转除气法应用最为广泛,但除气效率仍有待提高.近年来关于旋转除气的研究主要集中在转子的研究与优化设计[6, 7]、除气参数优化等方面.旋转除气的控制参数有转子转速、除气温度、除气时间、气体流量等.其中转子转速和气体流量是最重要的参数,但其对除气效果的影响和机理还有待于进一步研究.由于转子在熔体中引起的对流和气泡的分散性不可见,水模拟在研究铝合金除气方面获得了应用.水模拟最大的特点是具有可视性,能够直观反映气泡在水中的破碎、分散和移动行为.本文通过熔体除气实验研究了转子转速和气体流量对除气效果的影响,通过水模拟的方法研究了其对熔体中气泡尺寸和分布的影响规律,揭示了转子转速和气体流量对除气效果的影响机理,获得了最优工艺参数范围.
1 实验材料和实验方法本实验采用2524铝合金(质量分数,%,Cu:4.0~4.5;Mg:1.2~1.6;Mn:0.45~0.7;Fe<0.12;Si<0.06;Ti<0.1;Al:余量).合金在100 kW中频感应炉中进行熔炼,在4 kW电阻炉中进行保温和除气处理.合金熔炼温度750~760 ℃,保温温度730~740 ℃,除气温度730~740 ℃.采用自行设计的小型石墨转子除气装置进行除气和水模拟实验.除气时石墨转子中通入高纯氩气.合金除气、扒渣后在保温炉中静置10 min,然后采用ALSCAN测氢仪和减压凝固测氢法进行氢含量的测定.水模拟实验在透明的有机玻璃制作的方形容器中进行.容器尺寸长280 mm,宽280 mm,高350 mm.采用高清晰数码摄像机记录气泡在水中的分散、破碎和移动情况.石墨转子转速在0~690 r/min连续可调,氩气流量在1~20 L/min连续可调.
2 结果与讨论 2.1 转子转速对除气效果的影响氩气流量控制在1 L/min,将石墨转子转速分别设置为280和690 r/min,不同转速下随着除气时间的延长,铝合金中氢含量的变化如图 1所示.
![]() |
图1 氢含量随除气时间的变化 Fig. 1 Variation of hydrogen concentration as a function of degassing time |
在转子转速为690 r/min的情况下,除气1 min,熔体中氢含量由0.210 mL/100 g Al降低到0.160 mL/100 g Al,随着除气时间的延长,氢含量进一步降低,但降低的速度逐渐变慢.除气10 min时氢含量降低到0.105 mL/100 g Al,除气时间延长至20 min,氢含量变化不大,降低到0.095 mL/100 g Al.转子转速为280 r/min的情况下,氢含量的变化趋势与转子转速为690 r/min时的情况基本相同.但是,相同除气时间的条件下,转速为280 r/min时的氢含量均明显高于转速为690 r/min时的氢含量.本研究范围内10到20 min是比较合适的除气时间范围,较高的转速获得较好的除气效果.
氢含量直接影响着合金中气孔缺陷的形成.图 2为2524合金除气前后凝固试样纵截面上气孔分布情况.图 2a、图 2b为除气前的试样,其中图 2a为在真空条件下(7 000 Pa)凝固试样,图 2b为空气中即1.01×105 Pa下凝固试样.除气前,氢含量为0.210 mL/100 g Al,空气中凝固试样有一些小气孔如图 2b中箭头所示,而在真空条件下凝固试样气孔则非常明显.在经过除气后(转速690 r/min,氩气流量1 L/min,除气时间10 min),如图 2c、图 2d所示,空气中凝固试样和真空条件下凝固试样均未观察到明显的气孔.
![]() |
图2
除气前后凝固试样纵截面
Fig. 2 Vertical section of samples with and without degassing
(a), (b)—除气前 (H: 0.210 mL/100 g Al); (c), (d)—除气后 (H: 0.105 mL/100 g Al); (a), (c)—真空条件下凝固 (7 000 Pa); (b), (d)—1.01×105 Pa下凝固. |
将石墨转子转速设定为690 r/min,除气时间10 min,不同氩气流量条件下除气效果如图 3所示.
![]() |
图3 氢含量随氩气流量的变化 Fig. 3 Variation of hydrogen concentration as a function of flow rate of Ar |
氩气由无到有,除气效果变化非常明显.随着氩气流量的增加,氢含量呈现先降低后增加的趋势.当氩气流量由3 L/min增加到5 L/min时,氢含量没有进一步降低反而有所增加,其中的原因将在后续水模拟实验中进行分析.
2.3 旋转除气过程的水模拟1) 转子转速对气泡尺寸和分布的影响.将氩气流量设为1 L/min,转子转速分别为0,140,280,410,550,690 r/min,结果如图 4所示.随着转子转速的增加,水中气泡一方面尺寸减小;另一方面气泡分布趋于均匀,并且分布范围增加.
![]() |
图4 转子转速对气泡尺寸和分布的影响 Fig. 4 Effect of rotor rotation speed on the size and distribution of bubbles (a)—0 r/min; (b)—140 r/min; (c)—280 r/min; (d)—410 r/min; (e)—550 r/min; (f)—690 r/min. |
气泡尺寸随着转速增加的变化如图 5所示.转子由静止到140 r/min,气泡尺寸变化不大.在140 r/min到410 r/min范围内,随着转速的增加气泡尺寸快速减小.当转速超过410 r/min后,转速增加,气泡尺寸进一步减小,但减小的幅度趋缓,特别是当转速由550 r/min提高到690 r/min时,气泡尺寸变化很小.
![]() |
图5 氩气泡尺寸随转子转速的变化 Fig. 5 Variation of Ar bubble size as a function of the rotor rotation speed |
转子转速对氩气泡分布区域具有重要的影响.当转速低于280 r/min时,氩气泡较大且主要影响到以转子中心线为中心轴线,以转子最低端为底面,到液面的如图 4a、图 4b、图 4 c中虚线所示圆柱或者圆台区域.当转速增加到410 r/min时,气泡的分布区域发生显著变化,气泡分布到如图 4d中虚线以上的整个区域,转速增加,影响的区域进一步增大.
氩气泡分布区域的体积分数随着转速的变化如图 5所示.可见转速低于280 r/min时,氩气泡对分布区域影响不大.在280~410 r/min之间,存在明显的转折点,影响区域快速增加.而高于410 r/min时,氩气泡影响区域的体积分数变化又趋缓.
在旋转除气过程中,气泡尺寸对除气效果具有重要影响.相同体积的氩气,气泡越小则总的表面积就越大,即氩气与熔体总的接触面积越大.熔体除气主要是通过熔体中的氢向氩气泡中扩散而实现,氩气与熔体的接触面积增加则除气速率增加.另外气泡尺寸还影响到气泡在熔体中的停留时间.气泡在熔体中的上浮速度符合斯托克斯定律:
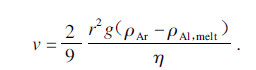
式中:ν是氩气泡的上浮速度;r是氩气泡的半径;ρAr氩气泡的密度;ρAl,melt是铝熔体的密度;η是铝熔体的黏度;g是重力加速度.
由此可见,气泡尺寸越小则在熔体中上浮的速度越慢,从而在熔体中的停留时间越长,有利于熔体中的氢向氩气泡中充分扩散.较高的转速增加氩气泡的数量,减小气泡的尺寸,增加气泡总的表面积,延长气泡在熔体中的停留时间,提高了气泡分布的均匀性,扩大了气泡作用范围,有利于获得较好的除气效果.转速280 r/min时气泡尺寸较大,作用范围较小;转速690 r/min时气泡尺寸较小,作用范围较大,所以如图 1所示,690 r/min时的除气效果较好.
结合熔体除气结果和水模拟结果,转子转速550~690 r/min是合适的转速范围,而10~20 min则是合适的除气时间范围.
2) 气体流量对气泡尺寸和分布的影响.转子转速固定在690 r/min,研究氩气流量对气泡及其分布的影响,结果如图 6所示.氩气流量由1 L/min增加到3 L/min,气泡尺寸变化不大,气泡影响的区域(图中虚线以上的区域)略有增加,液面也变化不大;提高氩气流量至5 L/min,则气泡尺寸开始增大,气泡影响的区域开始减少,液面上大气泡增多,液面气泡的破裂影响到液面的稳定;进一步提高氩气流量,则气泡尺寸增大,气泡影响的区域明显减小,液面由于较大气泡的溢出和破裂变得更加不稳定.
![]() |
图6 氩气流量对气泡尺寸和分布的影响 Fig. 6 Effect of flow rate of Ar on the size and distribution of bubbles (a)—1 L/min; (b)—3 L/min; (c)—5 L/min; (d)—10 L/min; (e)—15 L/min; (f)—20 L/min. |
气泡影响区域体积分数随着氩气流量增加的变化如图 7所示.可见气泡影响区域的体积分数在1~5 L/min的范围内先增加后降低,当氩气流量超过5 L/min后则迅速降低.这主要由于,气体流量较小时在转子的剪切作用下形成两相流,所以能将气泡均匀分布到各处.而当气体流量较高时,随着气体流量的增加,气体起到隔离转子与液体的作用,相当于在转子周围形成隔离膜,从而使气泡作用区域减小.氩气流量由1 L/min增加到3 L/min,总的气泡面积有所增加,气泡的作用区域有所扩大,所以如图 2所示,除气效果有所提高.而氩气流量由3 L/min增加到5 L/min,尽管气体流量增加了,但是气泡的尺寸有所增大,气泡的作用区域有所减小;另外由于熔体表面的波动引起吸氢的倾向增加,所以如图 3所示,氩气流量增加到5 L/min除气效果反而有所降低.在本研究的实验条件范围内,1~3 L/min是合适的氩气流量范围.
![]() |
图7 氩气泡影响区域体积分数随氩气流量的变化 Fig. 7 Variation of Ar bubble affecting volume fraction as a function of flow rate of Ar |
1) 转子转速对旋转除气过程具有重要影响,随着转子转速的增加,氩气泡的数量增多,尺寸减小,分布的均匀性提高,作用范围增大,除气效果提高.转子转速550~690 r/min是合适的转速范围.
2) 氩气流量对旋转除气效果也具有重要的影响,氩气流量由1 L/min提高到5 L/min,除气效果先提高后降低.这主要与气泡作用区域、气泡尺寸以及熔体液面波动的变化情况有关.在本研究的实验条件范围内,1~3 L/min是合适的氩气流量范围.
3) 采用小型旋转除气装置,高纯氩气流量1 L/min,转子转速690 r/min,除气20 min,能够将2524铝合金氢含量降低到0.10 mL/100 g Al以下.
[1] | Davis J R.ASM specialty handbook,aluminum and aluminum alloys[M].OH:ASM International,1993:199-231.(![]() |
[2] | Samuel A M,Samuel F H.Various aspects involved in the production of low-hydrogen aluminium castings[J].Journal of Materials Science,1992,27:6533-6563.(![]() |
[3] | Chaijaruwanich A,Dashwood R J,Lee P D,et al.Pore evolution in a direct chill cast Al-6 wt.% Mg alloy during hot rolling[J].Acta Materialia,2006,54(19):5185-5194.(![]() |
[4] | Chaijaruwanich A,Lee P D,Dashwood R J,et al.Evolution of pore morphology and distribution during the homogenization of direct chill cast Al-Mg alloys[J].Acta Materialia, 2007,55(1):285-293.(![]() |
[5] | Wang L,Guo E J,Huang Y C,et al.Rotary impeller refinement of 7075Al alloy[J].Rare Metals,2009,28(3):309-312.(![]() |
[6] | Warke V S,Shankar S,Makhlouf M M.Mathematical modeling and computer simulation of molten aluminum cleansing by the rotating impeller degasser part II.removal of hydrogen gas and solid particles[J].Journal of Materials Processing Technology,2005,168(1):119-126.(![]() |
[7] | Warke V S,Tryggvason G,Makhlouf M M.Mathematical modeling and computer simulation of molten metal cleansing by the rotating impeller degasser part I.fluid flow[J].Journal of Materials Processing Technology, 2005,168(1):112-118.(![]() |
[8] | Richly O.Vacuum degassing of aluminum melts[J].Aluminium, 1981,57(8):546-548.(![]() |
[9] | Iwamoto K,Yamasaki M,Kawamura Y.Vacuum degassing behavior of rapidly solidified Al-Mn-Zr alloy powders[J].Materials Science and Engineering A,2007,449/450/451(1/2):1013-1017.(![]() |
[10] | Zeng J M,Gu P,Wang Y B.Investigation of inner vacuum sucking method for degassing of molter aluminum[J].Materials Science and Engineering:B,2012,177(19):1717-1720.(![]() |