2.辽宁科技学院 冶金工程学院, 辽宁 本溪 117004;
3.宝山钢铁股份有限公司 炼铁厂, 上海 201900
2. Metallurgy Engineering College, Liaoning Institute of Science and Technology, Benxi 117004, China;
3. Ironmaking Plant, Baoshan Iron and Steel Co. Ltd., Shanghai 201900, China.
Corresponding author: FENG Ming-xia, E-mail:fengmingxia@gmail.com
高炉的日益大型化和复杂化使得高炉大修成本相当巨大,而炉缸、炉底的寿命是一代高炉寿命的限制性环节之一[1, 2, 3, 4].虽然高炉的炉龄大幅提高,但近几年也经常发生炉缸、炉底烧穿事故.由于高炉炉缸内始终存在渣铁而不能进行清空,使得其不能像其他部位那样,在生产过程中进行修补.因此,高炉炉缸、炉底的工作状态和寿命对于高炉获得良好的技术经济指标和延长高炉寿命都具有重要意义.通常对于炉缸侵蚀模型的研究主要分为两大类:一类为侵蚀机理解析模型[5, 6, 7],给出渣铁环流、出铁口深度、料柱是否沉坐等因素如何影响炉缸的侵蚀;另一类为炉缸侵蚀程度监测预报模型[8, 9, 10],给出炉缸当前侵蚀曲线及残厚形貌.本文提出一种利用埋入热电偶在线监测高炉 炉缸、炉底砖衬残余厚度的“边界移动”方法,将未知边界传热反问题转化成无约束最优化求解问题.依据数值传热学和有限元法建立高炉炉缸、炉底稳态传热数学模型,计算获得温度分布,以预埋热电偶反馈温度值为已知数据输入,采用最优化相关理论为基础,迭代求得可移动边界移动步长,经迭代计算输出炉缸内壁侵蚀形貌和炉衬残余厚度.
1 炉缸侵蚀监测模型 1.1 开发思路其基本原理为:使用“边界移动”的方法,将未知边界传热反问题转化成无约束最优化求解问题.具体求解过程:已知炉缸内衬形貌,基于炉缸炉底稳态传热数学模型计算得到温度场分布,与预埋热电偶反馈温度值比较,根据温度梯度,按最优化的梯度下降法计算移动步长因子和方向,进行边界移动,重新构造炉缸形貌;迭代计算直到预测温度和热电偶反馈温度满足指定精度,停止计算,输出炉缸内壁侵蚀形貌和炉衬残余厚度.流程计算图详见图 1.
![]() |
图1 高炉炉缸侵蚀监测模型流程图 Fig. 1 Flow chart of hearth erosion monitoring model for blast furnace |
建立的炉缸、炉底侵蚀监测模型主要包含三部分:炉缸温度场计算模块、最优步长计算模块和炉缸形貌构造模块,这三个模块为并列关系,分别负责计算不同的参数.温度场计算模块以炉缸传热数学模型为基础,使用有限元法进行不同形貌的炉缸温度场的计算和温度梯度的计算;最优步长计算模块以最优化理论为基础,进行最优步长的迭代计算;炉缸形貌构造模型根据最优步长移动内边界可移动点并将其依次连接构造成炉缸侵蚀残余形貌.
1.2 计算条件本文以典型的“陶瓷杯+碳砖”复合式高炉炉缸结构为原型,为说明模型的有效性又不至于使问题太复杂,对原型进行合理简化.图 2a给出了本文采用的目前被广泛使用的“陶瓷杯+碳砖”复合式炉缸、炉底结构,内层为刚玉预制块,即“陶瓷杯”;炉壁及炉底夹层采用微孔碳砖;炉缸底部采用普通碳砖,其各层的物理性能详见表 1.计算过程以炉缸、炉底耐火材料夹层中预埋热电偶的反馈温度为参考数据.图 2b为炉缸热电偶布置示意图,热电偶埋入微孔碳砖中,采用单层热电偶布置结构.本文采用有限元法进行温度场的求解计算.基本求解思想是把计算域划分为有限个互不重叠的单元,在每个单元内,选择一些合适的节点作为求解函数的插值点,将微分方程中的变量改写成由各变量或其导数的节点值与所选用的插 值函数组成的线性表达式,借助于变分原理或加权余量法,将微分方程离散求解.网格划分如图 2c所示,使用自适应网格划分方式,这种方法可以在某些计算精度要求较高的部位自动细化网格.
1.3 影响因子影响因子定义为:当炉缸内表面任意一个可移动节点i沿其温度梯度方向移动一个步长时,炉缸测温点温度值将产生变化,变化值分别为 Δti,1,Δti,2,…,Δti,13,将Δti,j称为影响因子.其物理意义为第i个节点缩进一个步长将对编号为j的热电偶造成温度波动.本文为说明问题,将炉缸、炉底内侧边界简化为共计20个可移动节点,预置热电偶数量为13个,因此每当20个可移动节点位置确定时,若需继续迭代,就要计算共13×20=260个影响因子.因此,要计算得出影响因子,就需计算炉缸温度场以及每次移动一个可移动点后的温度场.炉缸形貌因迭代每发生一次变化都需要计算一次影响因子,由于影响因子过多,在此不赘述.下面结合图 3a以未侵蚀时原始炉缸形貌为例,列出移动14号节点计算得出的影响因子进行解释说明.
![]() |
表1 炉缸材料的物理性能 Table 1 Physical properties of hearth materials |
![]() |
图2 “陶瓷杯+碳砖”炉缸炉底结构、热电偶布置及网格划分示意图 Fig. 2 Schematic diagram for hearth structure with ceramic cup and carbon brick, thermal couple arrangements and computation grids (a)—炉缸炉底结构; (b)—热电偶布置简图; (c)—自适应网格划分. |
图 3a为影响因子计算方法示意图.以14号节点为例,当14号节点沿其温度梯度负方向移动一个步长时(如图 3箭头所示),炉缸形貌将发生变化,因此温度场也会随之改变.如表 2所示,测温点处温度值会产生波动,因移动内边界节点而在测温点上产生的温差称作影响因子.
![]() |
图3 影响因子及最优步长计算方法示意图 Fig. 3 Schematic diagram for impact factor and the optimum step length (a)—影响因子计算方法; (b)—影响因子最优步长计算集合. |
将炉缸炉底内壁看作是由20个可移动的点按一定顺序依次连接的曲线,如图 3所示.而这20个点可以沿各自位置的温度梯度方向移动不同的步长,而步长的大小则需由最优步长计算模块计算得出.最优步长计算模块主要是根据最优化理论建立起来的,是整个高炉炉缸炉底侵蚀监测模型的关键部分.由温度场计算模型计算影响因子及测温处温度值,从而将不定边界传热反问题转化为最优化求解问题.
温度场计算模块计算出的影响因子为
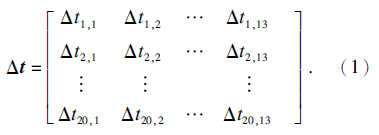
假设最优步长为


令F( P )=f1( P)+ f2( P)+,…,+ f13( P) ,现将最优步长 P =[p1,p2,…,p20]设为自变量,将F( P )设为目标函数,进行无约束最优化问题的求解.
![]() |
表2 初始时刻14号节点的影响因子 Table 2 Impact factor of number 14 node at initial time |
使用影响因子求解各节点最优步长的集合,此步长的集合能使各节点移动对每个测温点温度造成的叠加影响都最接近初始时刻与当前时刻热电偶温差.图 3为影响因子计算方法示意图.当10号热电偶当前实测温度与初始时刻(即炉缸未被侵蚀时)的温差不为零时,就需要移动内边界上可移动节点,可移动节点移动步长以移动后每个测温点温度造成的叠加影响都最接近初始时刻与当前时刻热电偶温差为准.当使用最优梯度法进行迭代求解时,若所求步长小于等于初始步长的20 % 时,迭代终止,将得到的最后值当作最优解输出.使用最优梯度法完成一次迭代后需重新构造炉缸炉型,并重新计算影响因子,再使用最优梯度法进行迭代求解.直到满足相邻两次迭代得出的所有测温点温差均小于等于1℃,整个循环过程终止.
1.5 炉缸形貌构造构造机理是将有限个节点按顺序依次连接构造成线;再将这些线按顺序连接,围成平面;最后将各个平面连接在一起就形成了炉缸模型.构造炉缸形貌最基本的要素是节点,可将这些节点分为可移动节点和不可移动节点两类:不可移动节点是指构造炉壁外侧、炉缸夹层、炉底底部的节点;可移动节点是指构造炉缸、炉底内壁侵蚀线的节点.可移动节点的移动量由两项参数确定,分别是移动方向和移动步长.移动方向即为温度场计算模块计算得出的节点处温度梯度方向;移动步长即为最优步长计算模块计算得出的最优步长.可移动节点经过移动后按照编号1~20的顺序依次连接,并与不可移动节点连接成的线按次序连接即可形成炉缸侵蚀形貌.
2 模型可靠性及误差讨论为了验证模型的可靠性和确认计算结果误差,本文构造了一个已经被侵蚀的高炉炉缸形貌作为样本,并计算其温度场,将侵蚀样本测温点温度记录下来,然后输入侵蚀监测模型中进行计算分析,将计算得出的炉缸侵蚀形貌以及炉衬残余厚度与样本进行对比分析.构造样本时考虑到高炉通常会发生不均匀侵蚀的情况,因此构造样本时将对高炉炉缸在工作状态下的实际炉壁残余厚度的情况进行模拟.将炉壁与炉底交界处设计为侵蚀比较严重的情况,而随着炉壁高度的增加,侵蚀状况有所减轻,炉衬被侵蚀的厚度逐渐减小.靠近炉壁一侧炉底侵蚀比较剧烈,砖衬残余厚度较小,靠近炉缸中心线一侧炉壁侵蚀较弱,砖衬残余厚度与初始时刻相比变化不大.图 4给出了样本炉缸的侵蚀形貌和温度分布云图,其中测温点温度由表 3列出.
![]() |
图4 样本炉缸的侵蚀形貌及温度场分布图 Fig. 4 Temperature field distribution and lining erosion profile of the sample hearth (a)—样本侵蚀形貌; (b)—样本温度分布. |
![]() |
表3 测温点温度值对比 Table 3 Comparison of temperatures at measurement points ℃ |
由表 3可以看出,随着迭代的进行,测温点温度值从初始状态开始越来越接近样本温度.当迭代4次后收敛,温度值变化不大.
表 4列出了炉衬残余厚度计算结果,可以看出计算得出的炉衬残余厚度沿高度和径向的变化趋势与样本基本相同.相对误差的平均值为3.6 % ,说明模型具有较高可靠性.
![]() |
表4 炉衬残余厚度计算结果 Table 4 Computational results of the inner lining residual thickness |
1) 以预置热电偶反馈温度为主要数据,使用最优化理论联合炉缸“边界移动”的方法,建立了计算炉衬残余厚度和炉缸侵蚀形貌的模型.
2) 使用建立的高炉炉缸侵蚀监测模型计算炉缸残余形貌和厚度,通过使用样本对模型可靠性和准确程度进行分析,相对误差平均值为3.6 % .此模型能够较精确计算出炉缸炉底侵蚀残余边界.
3) 建立最优化数学模型,将未知边界传热反问题转化为最优化求解问题是有效的.
[1] | Liu Z J,Zhang J L,Zuo H B,et al.Recent progress on long service life design of Chinese blast furnace hearth [J].ISIJ International,2012,52(10):1713-1723.(![]() |
[2] | Zhang F M.Design and operation control for long campaign life of blast furnaces [J].Journal of Iron and Steel Research International,2013,20(9):53-60.(![]() |
[3] | Johnny B,Henrik S.Model for fast computation of blast furnace hearth erosion and buildup profiles [J].Industry & Engineering Chemistry Research,2008,47(20):7793-7801.(![]() |
[4] | Shinotake A,Nakamura H,Yadoumaru N,et al.Investigation of blast furnace hearth sidewall erosion by core sample analysis and consideration of campaign operation [J].ISIJ International,2003,43(3):321-330.(![]() |
[5] | Huang C E,Du S W,Cheng W T.Numerical investigation on hot metal flow in blast furnace hearth through CFD [J].ISIJ International,2008,48(9):1182-1187.(![]() |
[6] | Guo B,Maldonado D,Zulli P,et al.CFD modelling of liquid metal flow and heat transfer in blast furnace hearth [J].ISIJ International,2008,48(12):1676-1685.(![]() |
[7] | Yu Z,Rohit D,Cheng Q Z,et al.Numerical analysis of blast furnace hearth inner profile by using CFD and heat transfer model for different time periods [J].International Journal of Heat and Mass Transfer,2008,51(2):186-197.(![]() |
[8] | 陈良玉,李玉,王子金,等.传热边界逆解在高炉炉缸侵蚀诊断中的应用[J].东北大学学报:自然科学版,2009,30(8):135-1138. (Chen Liang-yu,Li Yu,Wang Zi-jin,et al.Application of inverse solution to boundary of heat transfer in erosion diagnosis of blast furnace hearth[J].Journal of Northeastern University:Natural Science,2009,30(8):1135-1138.)(![]() |
[9] | 石琳,程素森,左海滨.高炉炉衬侵蚀边界识别的数值模拟[J].钢铁研究学报,2006,18(4):1-5. (Shi Lin,Cheng Su-sen,Zuo Hai-bin.Numerical simulation of erosion boundary identification of blast furnace lining[J].Journal Iron and Steel Research,2006,18(4):1-5.)(![]() |
[10] | Zagaria M,Dimastromatteo V,Colla V.Monitoring erosion and skull profile in blast furnace hearth[J].Ironmaking & Steelmaking,2010,37(3):229-234. (![]() |