2. 中国第一汽车股份有限公司 技术中心, 吉林 长春 130011;
3. 青岛征和工业有限公司, 山东 青岛 266705
2. R&D Center, China FAW Co., Ltd., Changchun 130011, China;
3. Qingdao CHOHO Industry Limited Company, Qingdao 266705, China.
Corresponding author: CHENG Ya-bing, E-mail: chengyb@jlu.edu.cn
混合动力汽车的动力系统包括多种动力源,一般多是内燃机和电动机两种,因此混合动力汽车兼并了发动机和电动机两种动力的优点.具有尾气排放少、燃油效率高、加速良好、运行安静等优点,在混合动力构型中,电机与变速箱平行布置的型式,节油效果能够达到35%以上,成为轿车混合动力的主要开发型式[1, 2].
本文研究的轿车混合动力用Hy-Vo齿形链,具有变节距和内-外复合啮合的双重效用,特别适用于在高速、变速、变载的工况,实现混合动力构型中电动机和变速箱之间的动力传递[3].在完成了Hy-Vo齿形链的参数计算之后,若干节内啮合链节+若干节外啮合链节依次交替连接,最后首尾铆接而成,通过对电机轴链轮和变速箱轴链轮进行围链,从而完成混合动力用Hy-Vo齿形链磨损试验传动系统的布置.
本文对混合动力Hy-Vo齿形链系统进行理论啮合设计,结合具体实例完成轿车混合动力Hy-Vo齿形链参数计算以及传动系统布局设计,并在磨损试验台上进行高速磨损试验,绘制Hy-Vo齿形链磨损曲线,并对磨损部位进行微观扫描分析.通过对混合动力用Hy-Vo齿形链进行磨损试验,分析其磨损特性,并通过对链板、销轴进行微观形貌分析,研究其磨损机制,从而为我国汽车链传动系统的设计研究提供切实可行的技术支撑,实验结果进一步验证了根据混合动力Hy-Vo齿形链理论设计方法所设计的Hy-Vo齿形链符合轿车混合动力传动系统对Hy-Vo齿形链的要求.
1 混合动力用Hy-Vo齿形链啮合设计 1.1 混合动力Hy-Vo齿形链设计在混合动力Hy-Vo齿形链拉直状态时建立坐标系,如图 1所示,定义P为混合动力Hy-Vo齿形链的基本节距,α为工作链板的齿形角,A为工作链板孔基准圆的圆心距,f为工作链板的基准边心距,γ为定位偏置角,r为销轴大端表面的曲率半径,Sm为链板孔基准圆圆心至异型销轴大端表面的距离,δ为内啮合链板内侧工作齿廓伸出量.
![]() | 图 1 Hy-Vo齿形链工作链板拉直状态 Fig. 1 The straighten state of the novel Hy-Vo silent chain |
拉直状态时其节距[4]变为
取内啮合工作链板内侧工作齿廓曲率为R,内侧工作齿廓曲率中心的坐标为
其中,f′=f-(P′-A)cosα.
1.2 混合动力链轮设计在混合动力传动系统运行的过程中,将混合动力Hy-Vo齿形链板与链轮的啮合视为直线齿廓的齿条刀具和链轮的啮合.齿条刀具进行变位时以刀具的分度线与链轮的分度圆相切作为加工基准,从而建立混合动力Hy-Vo齿形链-链轮-刀具齿条的Hy-Vo齿形链啮合设计体系.以链轮中心为坐标原点,链轮轮齿的对称中心线为纵坐标,过链轮的中心且垂直链轮轮齿对称中心线的水平直线为横坐标建立坐标系,如图 2所示.
![]() | 图 2 Hy-Vo齿形链-链轮-刀具齿条设计体系 Fig. 2 The design system of the new Hy-Vo silent chain-sprocket-hob |

当Hy-Vo齿形链转过2θ=2π/z时,节距[4]为
边心距[4]变为
初始边心距[4]为
从而可得出刀具的变位系数[4]为
链轮的量柱测量距[4]为
选取混合动力Hy-Vo齿形链的基本节距P=9.525 mm,工作链板的齿形角α=30°,工作链板孔基准圆的圆心距A=8.75 mm,链板的基准边心距f=4.68 mm,定位偏置角γ=5°,销轴大端表面的曲率半径r=7.5 mm,链板孔基准圆圆心至异型销轴大端表面的距离Sm=0.42 mm,根据式(1)可求得:P′=A+2[(r+Sm)cosγ-r]=9.529 7 mm.
令伸出量δ=0.10~0.30 mm,取内啮合工作链板内侧工作齿廓曲率为R=93 mm,λ=1.6°,根据式(2)求得内侧工作齿廓曲率中心的坐标为x1=78.08,y1=42.28.
选取直线链轮节距P1=9.525 mm,齿楔角α1=60°,刀具节距P2=9.525 mm,刀具齿形角α2=α=30°,量柱直径dR=6 mm.
当链轮齿数z=21时,根据式(3)求得节距.
根据式(4)求得边心距

根据式(5)求得初始边心距:

根据式(6)求得刀具的变位系数:
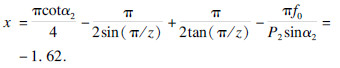
根据公式(7)求得链轮的量柱测量距:
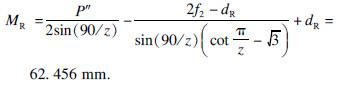
当链轮齿数z=25时,同理求得x=-1.57,MR=75.224.
3 混合动力Hy-Vo齿形链系统磨损试验 3.1 混合动力Hy-Vo齿形链系统布局设计根据上述混合动力Hy-Vo齿形链设计实例,选择电机轴链轮齿数z1=21,轮齿朝上,变速箱轴链轮齿数z2=25,齿槽朝上建立模型,链条节数LP=74节,上边及下边分别为26个链节长,在试验张紧力的作用下,链条上下两边都为紧边,见图 3.
![]() | 图 3 混合动力链传动系统布局设计 Fig. 3 The drive system of the novel Hy-Vo silent chain |
磨损试验设备是3MME磨损试验机,在力流式链条高速试验台上进行,如图 4所示,试验过程中电机轴链轮的转速为n=5 000 r/min,功率P=8.37 kW,链条的单边张力F=500 N,试验的样品数量为2条,润滑条件为喷油润滑.试验时间为300 h,开始试验13.5 h后进行第一次测量,以后每隔23.5 h进行一次测量.
![]() | 图 4 新型Hy-Vo齿形链高速磨损试验台 Fig. 4 The high-speed wear test rig of the new Hy-Vo silent chain |
由试验所测量的数据计算出中心距伸长量Δ=a-a0,a为试验中测量的实际中心距,a0为初始中心距,在本试验中a0=233.720 mm,得到如图 5所示试验时间与中心距伸长量的曲线关系图,从图中可以看出Hy-Vo齿形链在经过300 h的高速磨损试验后,中心距伸长量Δ=0.760 mm.
![]() | 图 5 Hy-Vo齿形链中心距伸长量曲线 Fig. 5 The center distance elongation curve of the new Hy-Vo silent chain |
在评价链条磨损性能时需计算磨损伸长率ε,本文中采用“中心距-链长”[5]的方法求ε,称为中心距磨损伸长率,即ε=Δa0×100%,通过对得到的试验数据进行研究与分析从而绘出混合动力用Hy-Vo齿形链在正常磨损过程中的中心距磨损伸长率ε与工作时间t的关系曲线,见图 6.
![]() | 图 6 新型Hy-Vo齿形链磨损伸长率曲线 Fig. 6 The wear elongation curve of the new Hy-Vo silent chain |
从图 5和图 6可以看出,0~50 h 显示的是初期磨损阶段,该曲线的斜率较大,这主要和齿形链的制造过程中留下的毛刺和装配空隙有关.曲线中的100~150 h 和 225~275 h 两段时间内磨损伸长量几乎没有变化,这期间磨损仍然在进行,只是异型销轴和链板在磨损试验的进行中存在疲劳裂纹的生成,但碎屑还没有剥落,产生了没有磨损的假象.此外,在300 h的磨损试验中,总的中心距磨损伸长率ε=0.325%,显示了Hy-Vo 齿形链的较高的耐磨特性,而0~50 h的磨损初期伸长量占 70%左右,而 50~300 h 期间磨损量占 30%左右,由此可知提高链条的制造精度并严格保证装配精度对于提高链条的使用寿命具有重大的现实意义[6].
4.2 Hy-Vo齿形链的磨损形貌利用XL30W/TMP扫描电子显微镜分别对Hy-Vo齿形链链板、异型销轴的磨损光亮位置进行微观扫描分析,其中,链板材料为50CrVA,异型销轴材料为20CrNiMo.
由图 7和图 8可看出,内啮合链板的内侧外凸曲线齿廓与外啮合链板的外侧直线齿廓均出现剥落坑,即点蚀,其磨损机制主要为疲劳磨损.在高速传动过程中,Hy-Vo 齿形链链板与链轮在接触表面产生相对滑动,使得链板与链轮接触处产生较大的循环应力,并发生塑性变形,从而在Hy-Vo 齿形链链板与链轮接触位置造成点蚀.从图 7,图 8的对比中可以看出,内啮合链板的内侧外凸曲线齿廓磨损比较严重,因而在传动过程中内啮合链板受到的力较大,承担了系统的大部分载荷,为提高内啮合链板的硬度,应对其进行特殊的强化处理[7, 8].
![]() | 图 7 内啮合链板的内侧外凸曲线齿廓磨损形貌 Fig. 7 The wear appearance of the inner meshing link joint inside flank |
![]() | 图 8 外啮合链板的外侧直线齿廓磨损形貌 Fig. 8 The wear appearance of the outer meshing link joint outside flank |
由图 9可以看出,在两个对滚异型销轴工作曲面上出现了与摩擦方向一致的沟槽,即犁切现象,工作曲面上伴随着剥落坑,从而说明异型销轴的磨损机制主要为磨粒磨损和疲劳磨损.对滚异型销轴在接触面产生高应力的冲击,在接触表面形成磨粒,磨粒受到的力可分解为垂直表面和平行表面的力[9, 10],垂直的分力将使磨粒压入异型销轴的接触面内,平行分力使磨粒在接触面做切向运行,从而引起异型销轴工作曲面的切变形和断裂.
![]() | 图 9 对滚异形销轴大端工作曲面的磨损形貌 Fig. 9 The main surface wear morphology of the special-shaped pin |
由图 10和图 11显示的磨损形貌可以看出,对滚异型销轴与链板孔的定位接触部位发生微动磨损,起初异型销轴与链板孔接触部位发生小振幅的相对运动,间隙增大,这有利于润滑油的进入和油膜的形成,并且能起到良好的散热作用,随着磨损的加剧,可能导致Hy-Vo齿形链松动、功率损耗以及噪声增大[11].
![]() | 图 10 链板孔定位接触部位的磨损形貌 Fig. 10 The wear appearance of the link joint hole |
![]() | 图 11 对滚异形销轴圆弧定位面的磨损形貌 Fig. 11 The circular arc locating surface’s wear appearance of special-shaped pin |
1) 通过建立混合动力Hy-Vo齿形链-链轮-刀具齿条三者之间的啮合设计体系,实现Hy-Vo齿形链与链轮的正确啮合传动,满足轿车混合动力传动系统中电机轴与变速箱轴的耦合传动.
2) 由Hy-Vo齿形链的磨损曲线可以得出:Hy-Vo齿形链及链轮具有良好的耐磨特性,根据Hy-Vo齿形链啮合理论所设计的Hy-Vo齿形链符合轿车混合动力传动系统对链条高转速、强耐磨的要求.
3) 在混合动力Hy-Vo齿形链高速传动过程中,磨损机制主要有疲劳磨损、磨粒磨损以及微动磨损,内啮合链板承受的循环应力较大,提高链条的制造精度并严格保证装配精度对于提高链条的使用寿命具有重大的现实意义.
[1] | Zhang J L,Yin C L,Zhang J W.Design and analysis of electro-mechanical hybrid anti-lock braking system for hybrid electric vehicle utilizing motor regenerative braking[J].Chinese Journal of Mechanical Engineering(English Edition),2009,22(1):42-49.(![]() |
[2] | Stephenson R,Glennie D,Fawcett J N,et al.A method of measuring the dynamic loads in high-speed timing chains[J].Journal of Automobile Engineering,2000,214(2):217-226.(![]() |
[3] | Meng F Z,Zhang J P,Huang M,et al.Research on wear characteristics of automotive engine chains under multi-cycle impact[J].Tribology,2007,27(6):573-577.(![]() |
[4] | 孟繁忠.齿形链啮合原理[M].北京:机械工业出版社,2008:35-44.(Meng Fan-zhong.The theoretic meshing of silent chain[M].Beijing:China Machine Press,2008:35-44.)(![]() |
[5] | Meng F,Liu X,Xu S.Meshing analysis and design of rotundity-datum-aperture Hy-Vo silent chain[J] . Proceedings of the Institution of Mechanical Engineers.Part C:Journal of Mechanical Engineering Science,2008,222(7):1297-1303.(![]() |
[6] | 王淑坤,孟繁忠,徐秀琴,等.汽车发动机滚子链的疲劳可靠性试验研究[J].中国机械工程学报,2009,20(21):2642-2645.(Wang Shu-kun,Meng Fan-zhong,Xu Xiu-qin,et al.Fatigue reliability test study of automobile engine roller chain[J].Chinese Journal of Mechanical Engineering,2009,20(21):2642-2645.) (![]() |
[7] | Meng F Z,Li C,Cheng Y B.Proper conditions of meshing for Hy-Vo silent chain and sprocket [J].Chinese Journal of Mechanical Engineering ,2007,20(4):57-59.(![]() |
[8] | Meng F Z,Wang S K,Lan H,et al.Wear failure mechanism and multi-impact property of automotive engine chain [J].Chinese Journal of Mechanical Engineering,2005,18(3):401-404.(![]() |
[9] | Cheng Y B,Meng F Z,Xu H X,et al .Experiment study on high-speed characteristics of automotive engine oil-pump chain [J].Chinese Journal of Mechanical Engineering,2007,20(1):36-39.(![]() |
[10] | 郑林庆.摩擦学原理[M].北京:高等教育出版社,1994:317-364.(Zheng Lin-qing.Principles of tribology[M].Beijing:Higher Education Press,1994:317-364.)(![]() |
[11] | Meng F Z,Feng Z M,Chu Y X.Meshing theory and design method of new silent chain and sprocket [J].Chinese Journal of Mechanical Engineering(English Edition),2006,19(3):425-427.(![]() |